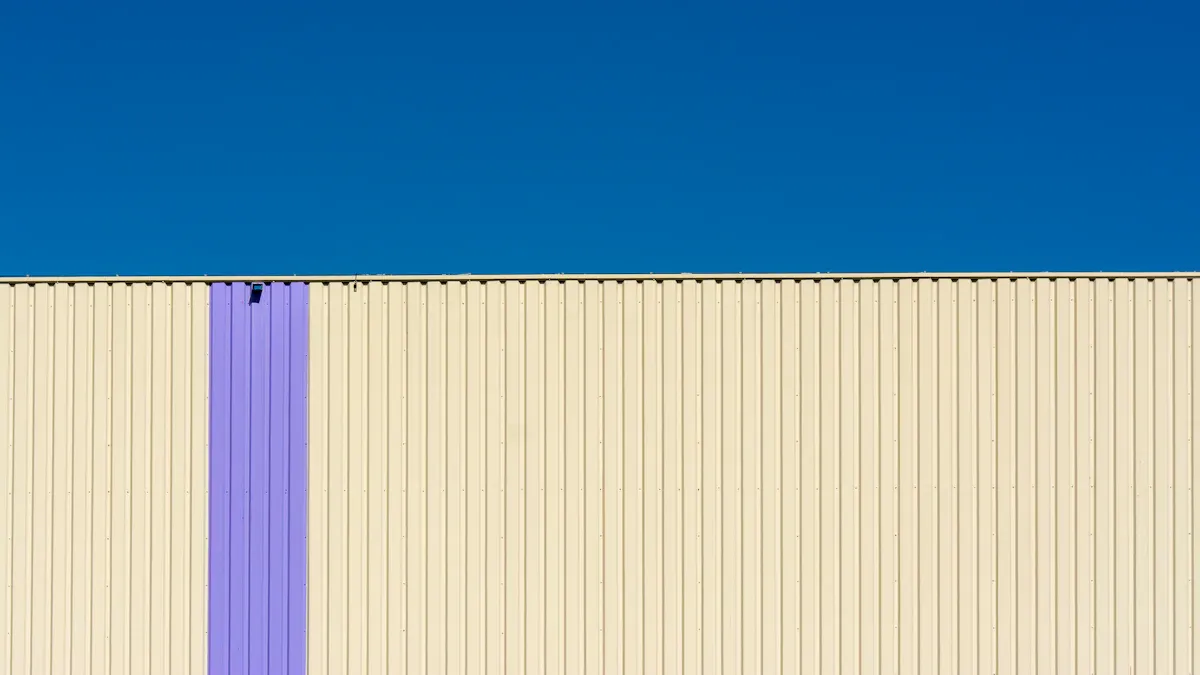
A sandwich panel is a building material made of three layers. It has two outer layers and a core in the middle. This design offers many benefits, making it popular in construction.
- About 28% of sandwich panels are used for building walls.
- Around 22% are used for roofs.
- Cold storage uses about 18% of these panels.
Sandwich panels are often used for walls because they insulate well, are easy to install, and are strong. They are light but tough, making them great for outside walls in homes, offices, and factories.
These panels are strong, insulate well, and are lightweight. For example, PUR Bs2 Sandwich Panels are known for keeping heat in and being light, taking up 10% of the market. EPS Sandwich Panels, used 14% of the time, are cheaper and also insulate well.
Key Takeaways
- Sandwich panels have three parts: two strong outer layers and a middle layer for insulation. This helps save energy in buildings.
- Using sandwich panels can lower heating and cooling bills by up to 70%. They are a budget-friendly option for building projects.
- These panels are light, making them easy to move and install. This can make construction faster.
- Sandwich panels can be used in many ways. They work for homes, cold storage, and even vehicles.
- Picking the right middle material, like foam or mineral wool, improves insulation and fire safety. This can match different project needs.
Composition of a Sandwich Panel
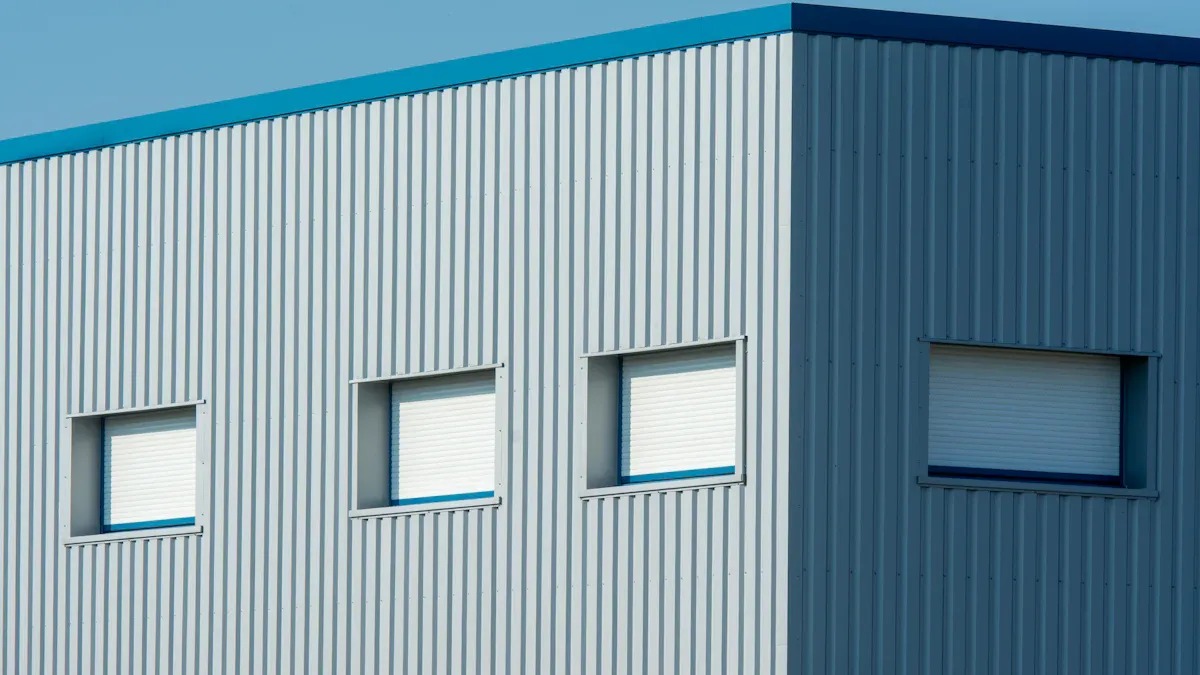
Outer Layers
Materials used (e.g., steel, aluminum)
The outer layers are made from strong materials like steel, aluminum, or fiberglass-reinforced plastic (FRP). Each has its own advantages. For example:
- Steel: Coated steel resists rust and handles tough weather well.
- Aluminum: It is light, doesn’t rust, and works in all climates.
- FRP: It is strong, light, and great for wet areas.
These materials keep the panel sturdy and dependable in many conditions.
Functions of the outer layers (e.g., protection, durability)
The outer layers protect the core and make the panel last longer. They block damage from impacts, sunlight, rain, and snow. This design helps the panel stay strong and in good shape.
Tip: Use stainless steel outer layers in food factories. They are easy to clean and hygienic.
Core Material
Common core materials (e.g., PIR, PUR, EPS, mineral wool)
The core is key to how the panel works. Common cores include:
- Polyurethane (PUR): Great for keeping heat in and saving energy.
- Polystyrene (EPS): A cheaper option for basic insulation needs.
- Mineral Wool: Resists fire and blocks noise, perfect for factories.
The core material depends on what the project needs.
Functions of the core (e.g., thermal and acoustic insulation)
The core keeps heat in and blocks noise. It helps save energy by keeping rooms warm or cool. For instance, polyurethane cores can lower energy use by 70%. Mineral wool cores also reduce sound, making spaces quieter.
Adhesive Layer
Role of adhesives in bonding layers
The adhesive layer sticks the outer layers to the core. It spreads stress evenly, making the panel stronger and more stable.
Types of adhesives used
Special adhesives like polyurethane or epoxy are used. These adhesives create a strong bond, even in tough conditions, helping the panel last longer.
Note: The adhesive layer is very important for keeping the panel strong over time.
Types of Sandwich Panels
Based on Application
Roofing Panels
Roofing panels keep heat in and block bad weather. They are light, so putting them on roofs is easy. These panels work well for factories, storage buildings, and homes. They last a long time, even in tough weather.
Wall Panels
Wall panels help save energy and block noise. They are used in homes and offices. These panels keep rooms warm or cool and lower energy bills. Wall panels are strong and come in different looks to match your style.
Facade Panels
Facade panels look nice and work well. They make building exteriors pretty while keeping them insulated. You can pick colors, textures, and designs to fit your building. These panels are popular for public places and modern offices.
Based on Core Material
PIR (Polyisocyanurate) Panels
PIR panels keep heat in and resist fire very well. They are great for roofs and walls where saving energy is important. These panels are trusted for big projects like factories and offices.
PUR (Polyurethane) Panels
PUR panels insulate well and resist fire a little. They cost less than PIR panels but work in similar ways. If you need good insulation for less money, choose PUR panels.
EPS (Expanded Polystyrene) Panels
EPS panels are light and cheap. They insulate well but don’t resist fire much. These panels are best for projects where saving money matters most.
Mineral Wool Panels
Mineral wool panels stop fires and block noise. They are great for risky places like factories and public buildings. These panels also keep heat in, making them useful for many projects.
Tip: Pick mineral wool panels for places needing fire safety and quiet spaces.
Core Material | Insulation Quality | Fire Safety | Best Uses |
---|---|---|---|
Polyisocyanurate (PIR) | Excellent | High | Roofs and walls |
Polyurethane (PU) | Good | Moderate | Cheaper option for PIR-like uses |
Mineral Wool | Good | High | Walls and soundproof areas |
Expanded Polystyrene (EPS) | Good | Low | Budget-friendly projects |
Each sandwich panel type has special features. Pick the one that fits your needs for insulation, fire safety, and cost.
Benefits of Sandwich Panels
Thermal Insulation
Energy efficiency in buildings
Sandwich panels help keep buildings energy-efficient. They provide great thermal insulation. Using these panels can improve energy use by 20% compared to regular materials. They keep indoor temperatures steady, so less heating or cooling is needed. Whether for homes or offices, they create a comfy space all year.
Reduction in heating and cooling costs
Better insulation means lower heating and cooling bills. Sandwich panels with polyurethane cores can cut energy use by 70%. This saves money on utilities over time. These panels are cost-effective because they reduce wasted energy and improve efficiency.
Lightweight and Durable
Ease of transportation and installation
Sandwich panels are light, making them easy to move and install. Prefabricated designs save time and effort during construction. For example:
- They weigh 25% less than regular materials, so they’re easier to carry.
- Prefabrication allows quick assembly, speeding up the building process.
This makes them perfect for projects with tight schedules.
Long-lasting performance
Sandwich panels are strong and last a long time. They handle bad weather like rain, snow, and wind without problems. Their tough design reduces wear and tear, so replacements aren’t needed often. This durability makes them reliable for many years.
Cost-Effectiveness
Lower material and labor costs
Sandwich panels are a budget-friendly choice for modern buildings. Prefabrication reduces waste and keeps quality consistent. Quick installation means fewer workers are needed, saving money. For instance:
- Prefabrication cuts material waste, lowering costs.
- Fast installation reduces labor expenses, saving money on-site.
Minimal maintenance requirements
New sandwich panels need little maintenance, cutting costs by 15%. They resist weather damage and wear, so upkeep is simple. Over time, this saves money, making them a smart choice for any project.
Benefit Type | Measurement/Impact |
---|---|
Energy Efficiency | Up to 20% better than regular materials |
Maintenance Costs | 15% lower due to improved panel designs |
Construction Time | Faster because of lightweight materials |
Cost-Effectiveness | Cheaper than traditional building options |
Tip: Use sandwich panels for projects needing energy savings, strength, and low costs.
Versatility
Customizable for various applications
A sandwich panel is very flexible for building needs. It works in modular buildings, unique designs, or temporary setups. You can change its size, thickness, or core to fit your project. For example, use fire-resistant panels for factories or light ones for prefab homes. This makes sure the panels work well in any place.
These panels are not just useful but also stylish. They are strong and modern, perfect for creative projects. Whether for cold storage or a fancy office, they combine function and design.
Aesthetic options for design flexibility
Sandwich panels also look great and are easy to customize. They come in many colors, textures, and finishes to match your style. For example, Tile Sandwich Panels offer Red Tile, Aged Albero, or Slate Grey. These choices make buildings look nice without losing strength or insulation.
Use these panels for a sleek office or cozy home. They mix design with function, making them popular with builders. By picking the right finish and color, you can make any building stand out.
Tip: Try textured finishes for a unique style while keeping the panel’s benefits.
Applications of Sandwich Panels
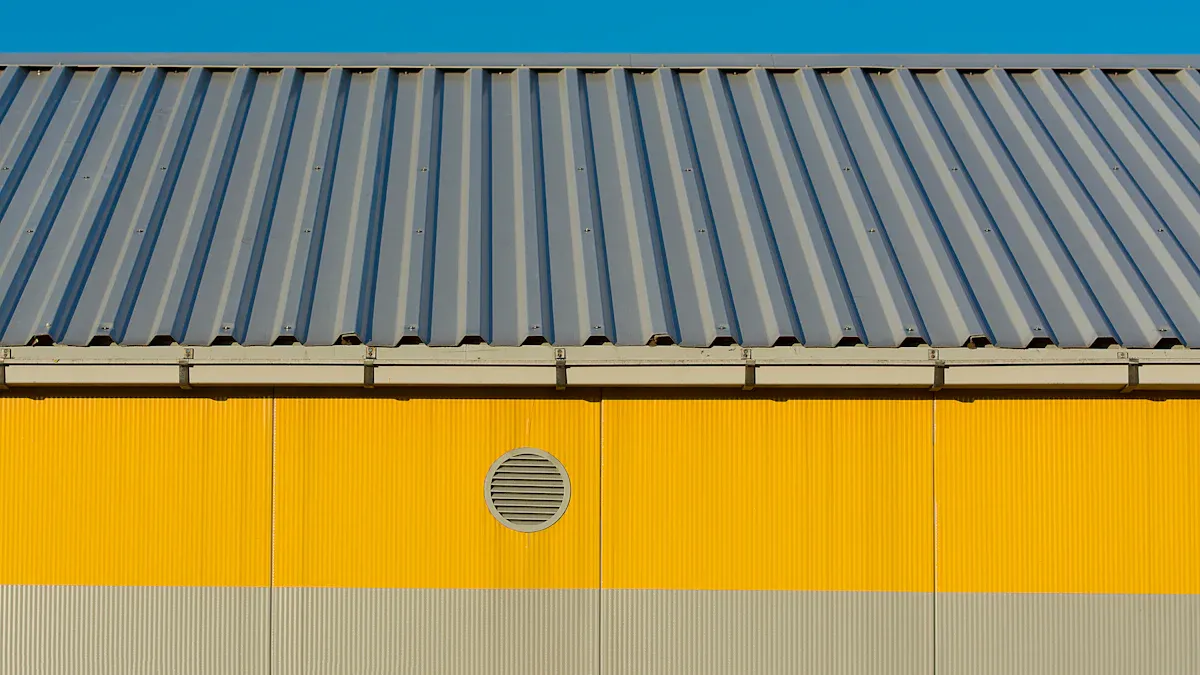
Construction Industry
Residential and commercial buildings
Sandwich panels are often used in homes and offices. They keep buildings energy-efficient by providing great insulation. These panels block fire and noise, making spaces safe and quiet. Use them for walls and roofs to save energy and keep indoor temperatures steady.
Did you know? Sandwich panels are eco-friendly because they can be recycled. Their light weight makes installation faster, cutting labor costs and waste.
Application | Percentage of Usage | Key Benefits |
---|---|---|
Building Wall | 28% | Energy-saving, fireproof, soundproof, improves indoor comfort. |
Building Roof | 22% | Great insulation, strong structure, reduces heat loss, quick to build. |
Industrial facilities
Factories and warehouses use sandwich panels for their strength and insulation. They handle tough conditions and work with many building designs. This makes them perfect for industrial projects.
Cold Storage
Refrigerated warehouses
Cold storage buildings need sandwich panels for their excellent insulation. These panels help control temperatures, saving energy and keeping goods fresh longer.
Metric | Description |
---|---|
Insulation Properties | Excellent insulation keeps energy use low. |
Optimal Temperature Control | Helps maintain the right temperature for cold storage. |
Food processing units
In food factories, sandwich panels keep the area insulated and dry. This creates a clean and safe space for storing and preparing food. Quick installation also reduces delays during construction.
Modular Buildings
Prefabricated homes
Prefabricated homes use sandwich panels because they are strong and insulate well. They make building faster and cheaper. You can adjust the panels to match your design needs, combining style and function.
Temporary structures
Temporary buildings like event halls or shelters use sandwich panels. These panels are light, strong, and block fire and noise. They create safe and comfortable spaces quickly.
Pro Tip: Choose sandwich panels for modular buildings to save time and money while ensuring quality.
Other Uses
Transportation (e.g., refrigerated trucks)
Sandwich panels are very important in transportation. They are used in refrigerated trucks to keep goods fresh. These panels provide great insulation for food and medicine during travel. Their light weight helps vehicles use less fuel, saving money on transport.
Aluminum honeycomb panels are often used in cars, buses, and military trucks. They are strong but light, making them perfect for heavy-duty jobs. Carbon fiber-reinforced plastic panels are also popular. They are tough and last long, even in hard conditions. These materials help vehicles stay strong and energy-efficient.
Fun Fact: By 2033, the sandwich panel market in transportation may grow to USD 18,058.33 million. It is expected to grow at a rate of 6.4% yearly from 2025 to 2033.
Aerospace and Marine Industries
In aerospace and marine industries, sandwich panels are very useful. They are strong but light and insulate well. These panels are used in airplanes, ships, and space projects. For example, thermoplastic core panels are common in planes and ships. They are stiff, resist fire, and are very safe.
Carbon fiber panels are great for these industries. They are strong, resist fire, and don’t get damaged by water or rust. This makes them good for space and deep-sea use.
Aspect | Details |
---|---|
Market Size | Could reach US$1.2 billion by 2026, growing 9.6% yearly from 2021-2026. |
Key Characteristics | Strong, light, insulates well, and very stiff. |
Applications | Used in cars, planes, and space projects. |
Specific Uses | Thermoplastic panels in planes, trains, and ships. |
Material Benefits | Carbon fiber panels are strong, fireproof, and resist water and rust. |
These panels make planes and ships light but safe. They are reliable and work well in tough conditions. Whether for air or sea, sandwich panels are efficient and durable.
Tip: Use carbon fiber sandwich panels for projects needing strength and weather resistance.
Sandwich panels are important in today’s building and industrial work. They help save energy, cut costs, and make building faster. Their light but strong design works well for homes, offices, and factories. As cities grow, more people want these panels for cheap and eco-friendly buildings.
Aspect | Details |
---|---|
Impact on Construction | Sandwich panels boost energy savings, lower costs, and speed up building, making them a top choice for homes, offices, and factories. |
Market Growth Drivers | The need for quick, low-cost building and affordable homes due to city growth is driving the demand for sandwich panels. |
Future Potential | Factories and big projects will use more panels because they need materials that are strong, light, and last long. |
Technological Advancements | New ideas like better insulation cores and stronger outer layers are making sandwich panels tougher and better at saving energy. |
Sustainability Trends | Green building rules and eco-friendly ideas are increasing the use of sandwich panels in big projects, with many builders using more of these materials every year. |
Think about using sandwich panels for your next building project. They save energy, last long, and cost less. Contact us to learn how they can help with your building needs.
FAQ
What are sandwich panels made of?
Sandwich panels have three layers: two outer layers and a core. The outer layers are strong and made from materials like steel or aluminum. The core gives insulation and can be made of polyurethane, mineral wool, or polystyrene.
What makes sandwich panels energy-efficient?
The core in sandwich panels keeps heat from moving through. It helps rooms stay warm in winter and cool in summer. This saves energy and lowers heating or cooling bills.
What types of sandwich panels are available?
Sandwich panels come in different types for various uses. Roofing, wall, and facade panels are common examples. Core materials like PIR, PUR, EPS, and mineral wool offer benefits like fire safety or being budget-friendly.
What industries use sandwich panels?
Many industries use sandwich panels, such as construction and cold storage. They are also used in modular buildings, transportation, and aerospace. Their light weight and strength make them useful for many jobs.
What are the benefits of using sandwich panels?
Sandwich panels are strong, insulate well, and save money. They are light, easy to set up, and need little care. You can also customize them to fit your project’s style and needs.
Tip: Use sandwich panels for projects needing quick setup and energy savings.