Weight Comparison is very important for how sandwich panels work. It affects how panels handle outside forces. For example:
How a panel reacts depends on the weight of an explosion hitting it.
With small blasts, the front and back bend almost the same.
With bigger blasts, the bending difference grows, showing that weight affects strength.
Understanding the weight comparison between Rockwool and other materials helps you choose the best one for your project, balancing strength and usability.
Key Takeaways
Rock wool panels are heavy but great for fire safety and noise control.
Lighter panels like polyurethane and EPS are simpler to move and set up. This saves time and lowers shipping costs.
Pick a panel based on your project’s needs, like insulation, strength, or easy setup.
Heavy panels might need more workers and special tools to install. Plan ahead for a smooth job.
Balance weight, price, and performance. Choose materials that fit your project goals best.
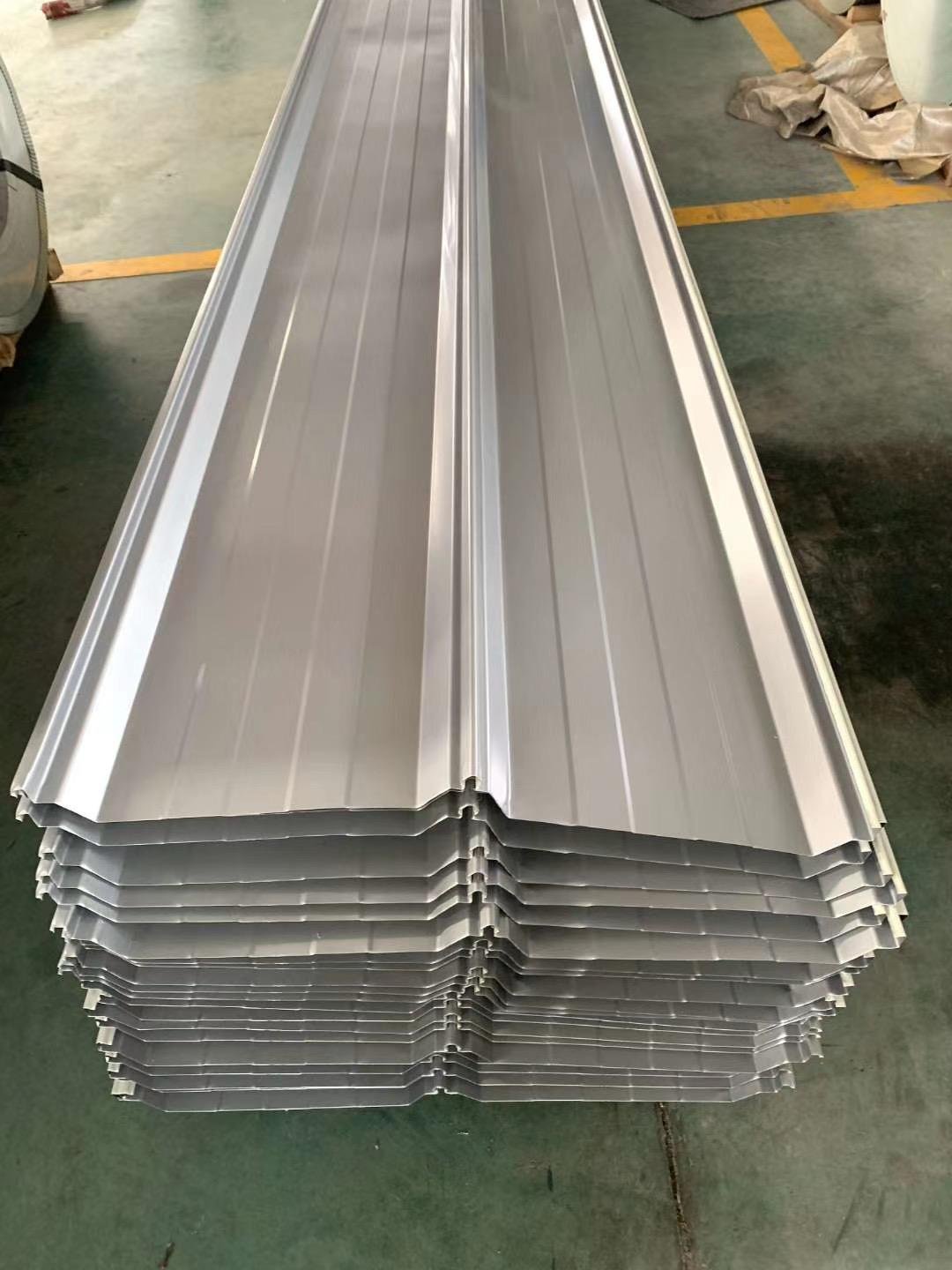
Rock Wool Sandwich Panel: Weight Characteristics
Density and weight properties
Rock wool sandwich panels are heavy because they are very dense. Their density usually ranges between 100 to 200 kg/m³. This depends on the type of product and its use. The dense core helps keep heat inside, saving energy. These panels weigh more than lighter options like EPS or PU panels. The extra weight comes from the tightly packed rock wool core. This core makes them better at stopping fires and blocking noise.
Tip: Think about how much insulation you need before picking rock wool panels.
Structural benefits of higher weight
The heavier weight of rock wool panels makes them stronger. They can hold more weight, which is great for tough jobs. For example, they work well in factories or places with bad weather. The weight also helps block sound, keeping spaces quieter. Plus, the dense core stops fire from spreading, making them safer for buildings with strict fire rules.
Challenges posed by weight
The heavy weight of rock wool panels can cause problems too. They are harder to move and need special tools or more workers to install. Shipping costs can also go up because they are bulky. If your project needs lightweight materials, these might not work. But with good planning, you can still use them and enjoy their great insulation benefits.
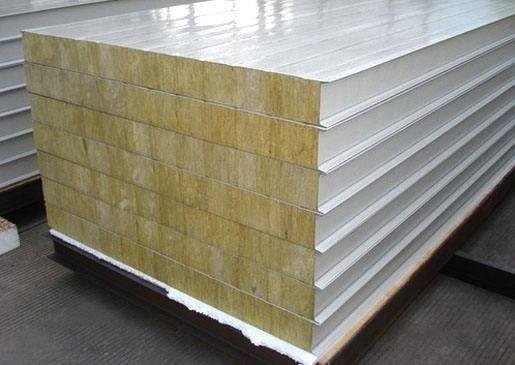
Weight Comparison: Rockwool vs Other Sandwich Panel Materials
Polyurethane (PU) Panels: Lightweight properties
Polyurethane panels are very light and easy to use. They usually weigh about 40 kg/m³, much less than rock wool panels. Their light weight makes moving and installing them simple. PU panels are great for projects needing less structural weight.
Even though they are light, PU panels insulate well. They help keep indoor spaces warm or cool, saving energy. But they don’t resist fire or block sound like rock wool panels. If you need easy installation and good insulation, PU panels are a smart choice.
Expanded Polystyrene (EPS) Panels: Density and weight comparison
EPS panels are another lightweight option. Their density is between 10 to 30 kg/m³. They are much lighter than rock wool panels, making them easy to transport and install. These panels are perfect for projects needing light materials.
EPS panels insulate fairly well but don’t stop fire or noise like rock wool. They work best in places with low fire risks. If you want a cheaper, lightweight option, EPS panels are a good pick.
Honeycomb Core Panels: Weight and rigidity
Honeycomb panels are strong and light at the same time. They are designed to be tough while staying lightweight. Research shows honeycomb panels absorb energy well under pressure. This makes them great for projects needing strength and low weight.
Honeycomb panels are lighter than rock wool panels but don’t insulate as well. They also don’t resist fire like rock wool. If you need both strength and lightness, honeycomb panels are a good choice.
Glass Wool Panels: Weight characteristics
Glass wool panels are a common choice for sandwich panels. They are lightweight, with a density of 50 to 100 kg/m³. These panels weigh less than rock wool but more than PU or EPS panels. Their weight is a good mix of easy handling and strength.
Glass wool panels insulate well by trapping air in their fibers. This reduces heat transfer and keeps indoor spaces comfortable. They are great for projects needing good insulation without too much weight. However, they don’t resist fire as well as rock wool panels. They can handle some heat but may fail in high fire-risk areas.
Their light weight makes moving and installing them simple. You can save time and labor costs during setup. Even though they are lighter, they still block sound fairly well, though not as much as rock wool. If you need insulation and easy installation, glass wool panels are a smart pick.
Comparative weight analysis table
Here’s a simple comparison of sandwich panel materials and their weights:
Material | Density (kg/m³) | Weight Features | Main Benefits |
---|---|---|---|
Rock wool sandwich panels | 100-200 | Heaviest | Best fire resistance and soundproofing |
40 | Very light | Great insulation, easy to use | |
EPS panels | 10-30 | Lightest | Cheap, decent insulation |
Honeycomb core panels | Varies | Light and strong | High strength with low weight |
Glass wool panels | 50-100 | Medium weight | Good insulation, simple to install |
This table shows how rock wool compares to other materials. While heavier, its fire resistance and soundproofing make it ideal for certain uses.
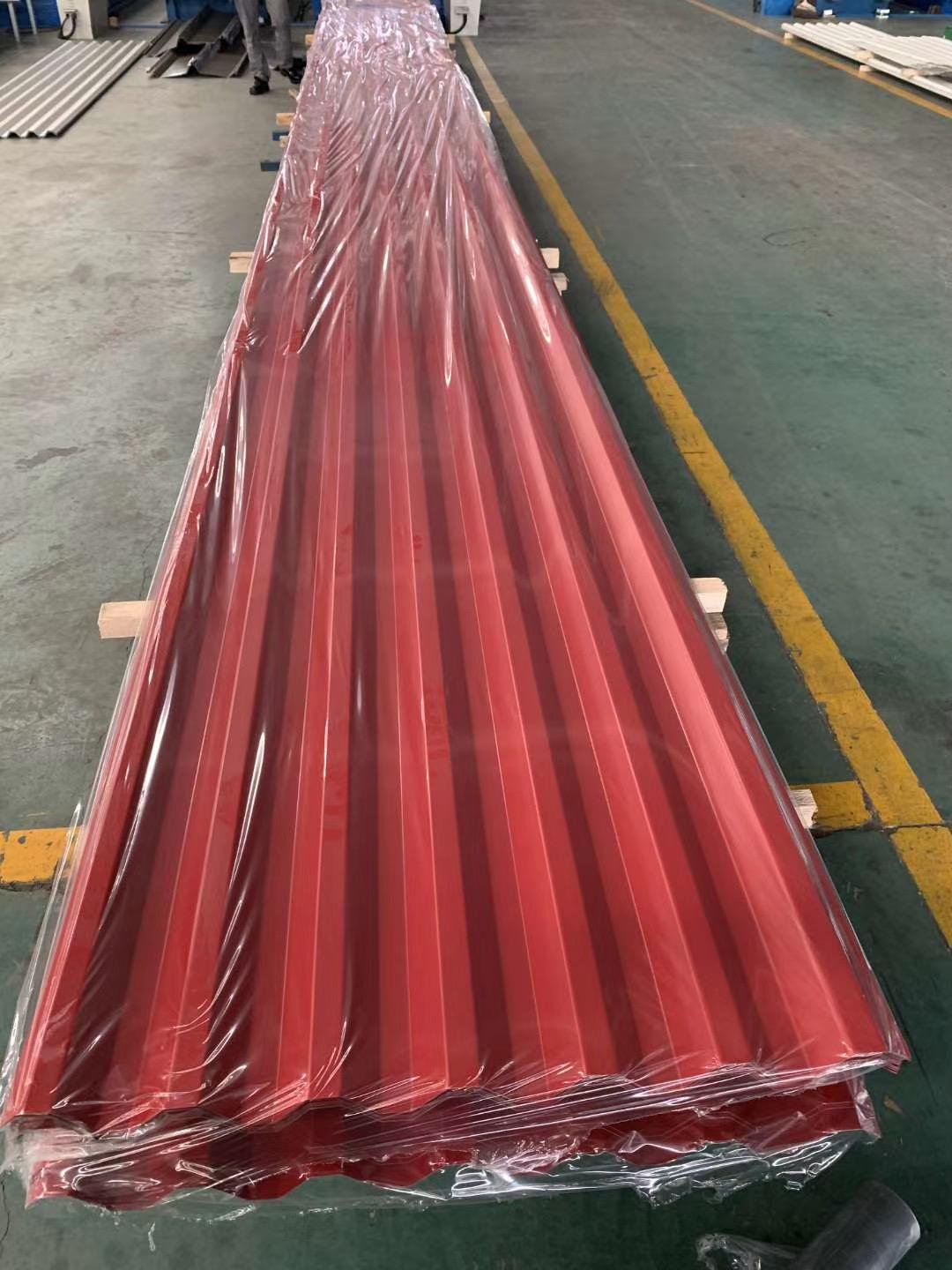
Impact of Weight on Installation, Transportation, and Application
Installation: Handling heavier materials
Rock wool panels are heavier and harder to install. You might need more workers or special tools like cranes. This can make installation take longer and cost more.
But the extra work is worth it. Rock wool panels are strong and safe. They insulate well and resist fire, which is great for tough projects. To make things easier, plan ahead. Have the right tools and team ready before starting.
Transportation: Logistics and cost considerations
Rock wool panels are heavy, so shipping them costs more. You may need bigger trucks or more trips, which uses more fuel. Lighter panels like polyurethane are cheaper and easier to move.
Studies show changing truck rules can save money. For example:
Changing traffic patterns saved over $5.5 billion in some cases.
Higher truck weight limits saved over $13 billion yearly by needing fewer trips.
Moving goods from trains to trucks changed costs, especially for cheap items.
If shipping far, think about how weight affects costs. Lighter panels save money, but heavier ones like rock wool are safer and insulate better.
Application suitability: Matching weight to project needs
Pick panels based on what your project needs. Rock wool panels are great for places needing fire safety, soundproofing, or insulation. They work well in factories, warehouses, or areas with bad weather.
If you want easy setup and lower costs, pick polyurethane panels. They are light, insulate well, and are simple to install. For temporary buildings or low-risk areas, EPS panels are a cheap and good choice.
Choose panels that match your project’s needs. This helps balance cost, performance, and ease of use.
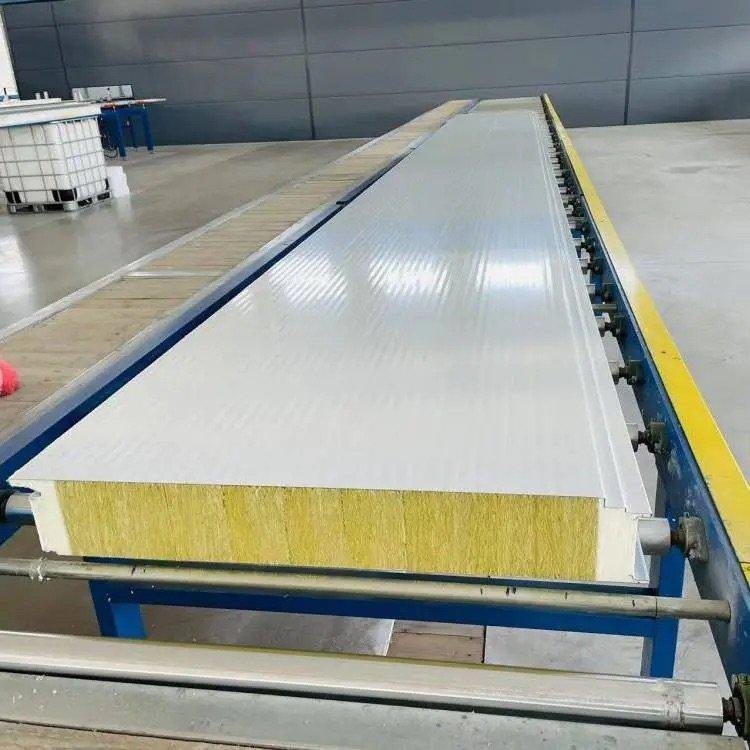
Decision-Making Guide: Picking the Best Sandwich Panel Material
Choosing based on weight
Weight is important when picking sandwich panel materials. Heavy panels like rock wool are great for fire safety and blocking noise. These features make them good for projects needing high safety or quiet spaces. But their weight can make moving and installing harder.
Lighter panels, like polyurethane ones, are easier to move and set up. Their light weight lowers shipping costs and makes handling simple. These panels work well for projects needing easy use, energy savings, and good heat insulation.
Think about what your project needs most. If fire safety and soundproofing matter, heavier panels are worth the effort. For faster and cheaper projects, lighter panels like polyurethane are a better choice.
Balancing weight, cost, and performance
It’s important to balance weight, cost, and how well panels work. Studies show lighter materials can save money and time in construction. For example, in offshore projects, lighter materials are easier to move and install, cutting costs. This idea works for sandwich panels too.
Polyurethane panels are light but still insulate heat and block water well. They are a good choice for saving energy and cutting costs. But they don’t block noise or resist fire as well as heavy rock wool panels.
When deciding, think about your budget, project needs, and limits. Light panels cost less to ship and install. Heavy panels last longer and are safer for tough jobs.
Knowing the weight differences of sandwich panels helps you choose wisely. Heavy panels like rock wool are great for fire safety and blocking noise. Lighter ones, like polyurethane and EPS, are easier to move and install.
Tip: Pick a panel weight that fits your project. For example, use rock wool for safe spaces or polyurethane for quick, budget-friendly setups.
When picking a material, think about weight, cost, and how it works. Decide what’s most important—insulation, strength, or easy handling. This way, your project will turn out the best.
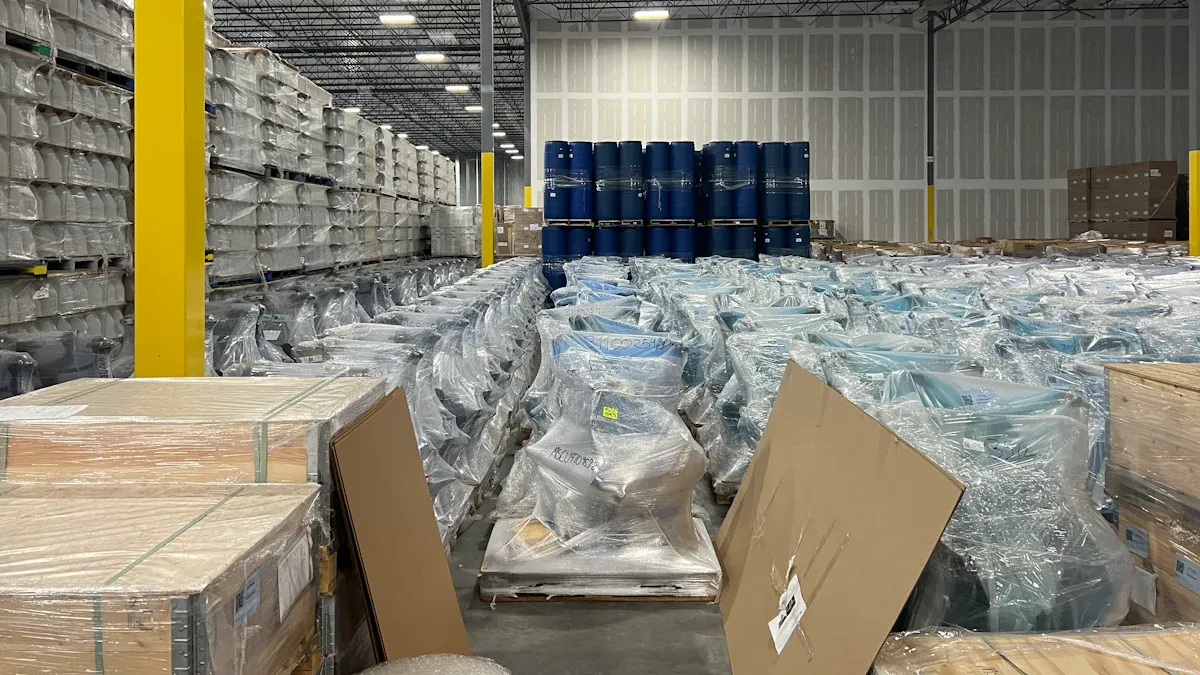
FAQ
Why are Rockwool panels heavier than other materials?
Rockwool panels are heavier because their core is tightly packed with mineral fibers. This makes them denser than lighter panels like EPS or PU. The extra weight helps them resist fire, block noise, and last longer.
Are lighter panels like EPS or PU weaker?
Lighter panels are strong enough for certain uses but not as tough as Rockwool. They are good for low-risk areas or temporary buildings. For harder jobs, Rockwool panels are stronger and work better.
How does weight affect shipping costs?
Heavier panels like Rockwool cost more to ship because they are bulky and heavy. Lighter panels like PU or EPS are cheaper to move, making them better for projects with smaller budgets.
Are heavy panels like Rockwool hard to install?
Rockwool panels take more effort to install because they are heavy. You might need extra tools or workers, like cranes, to help. Even though it’s harder, the benefits of Rockwool make it worth the effort.
Which panel is best for fire safety?
Rockwool panels are the safest for fire protection. Their dense core doesn’t burn and stops fire from spreading. Lighter panels like PU or EPS don’t protect as well against fire.