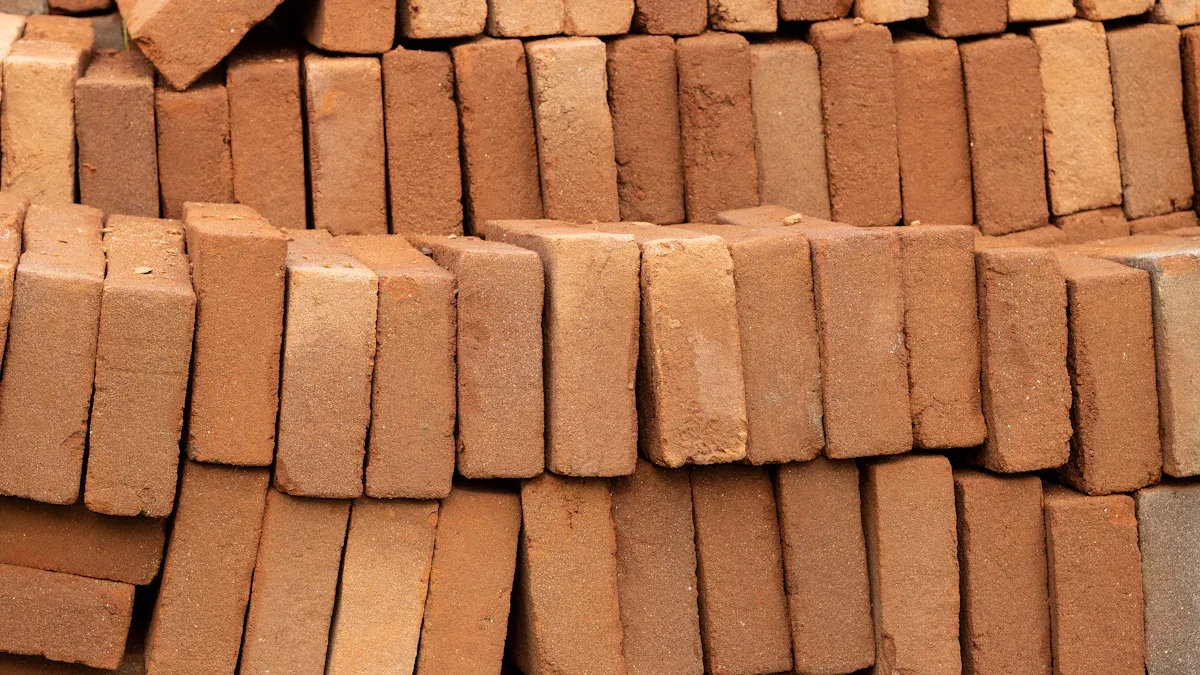
PU sandwich panels are known for their strength and durability, making them ideal for demanding applications. They feature a unique design that includes a foam core sandwiched between two metal layers, resulting in a lightweight yet robust structure. These panels can support heavy loads with a strength of 15.53 MPa and exhibit excellent resistance to bending with a strength of 3.68 MPa. Additionally, their tensile strength of 0.175 MPa ensures stability under pressure. These attributes contribute to their long-lasting performance in a variety of environments.
Key Takeaways
PU sandwich panels are light but strong, so they are easy to set up and can hold heavy weights.
The special foam inside and metal layers keep heat or cold in, saving energy in buildings and storage areas.
These panels do not get damaged by water or weather, lasting a long time in different environments.
PU panels can last 20 to 50 years and need little care, making them a budget-friendly option.
They can be used in building, cooling systems, and transport, fitting many industry needs.
Composition and Structure
Materials Used in PU Sandwich Panels
Polyurethane Core
The polyurethane (PU) core is the main part of PU panels. This foam is light, keeps heat out, and adds strength. It works well in places like cold storage where temperature control is needed. The foam doesn’t get squished easily, so it can hold heavy weights without bending.
The glue in the core is very strong. It keeps the foam stuck to the outer layers, even under pressure. This stops the layers from coming apart and keeps the panel strong. These features make the PU core a great choice for strength and keeping heat in or out.
Dual Metal Layers
The outside layers of PU panels are usually steel or aluminum. These metals protect the foam inside from damage and bad weather. They also make the panels stronger, so they don’t break when pulled.
The metal layers help the panels last longer. They keep water, sunlight, and temperature changes from harming the foam. Together, the foam and metal layers make a strong and durable panel.
Evidence Description | Detail |
---|---|
Tensile Strength | Panels stay strong when pulled, with a tensile strength of 0.175 MPa. |
Adhesive Strength | Strong glue keeps layers together, making the panel reliable. |
Insulation Properties | Foam blocks heat, perfect for places needing temperature control. |
Structural Integrity | Metal layers protect foam, letting panels hold heavy loads safely. |
Design Features Enhancing Strength and Durability
Lightweight and High Strength-to-Weight Ratio
PU panels are light but still very strong. This makes them easy to move and install. Even though they are light, they can hold heavy weights. Their lightness also lowers building costs and makes construction faster.
Bonding Between Layers for Structural Integrity
The foam sticks tightly to the metal layers. This strong bond stops the layers from coming apart, even under stress. The way the panels are made ensures the foam and metal stay connected. This keeps the panels strong for a long time.
Design Feature | Contribution to Durability |
---|---|
Outer Layers | Add strength and protect foam from damage |
Adhesive Layer | Stops layers from coming apart, keeping the panel strong |
Manufacturing Process | Makes sure foam and metal stick well, improving durability |
These materials and designs make PU panels a great choice for strength and long-lasting use.
Key Strength Properties
Load-Bearing Capacity
Resistance to Compression and Heavy Loads
PU sandwich panels are strong and handle heavy weights well. The foam core and metal layers make them tough. They can hold a lot of weight without bending or breaking.
Core Material | Compressive Strength (MPa) | Tensile Strength (MPa) | |
---|---|---|---|
PU Foam | 3.68 | 15.53 | 0.175 |
Tests show these panels handle pressure from all sides. Bending tests prove they absorb 21% more energy than other materials. This makes them great for holding heavy loads in many uses.
Resistance to Deformation
Flexural Strength and Dimensional Stability
PU panels stay in shape even when bent or stressed. Their bending strength helps them stay stable under pressure. Tests check how much stress they can take without breaking.
The foam and metal layers stick together tightly, adding strength.
Thicker panels, like 20 mm, hold 61.4% more weight than thin ones.
Stress on the foam and metal layers drops by 15.73%, keeping them safe.
These features help the panels stay strong and keep their shape in tough conditions.
Structural Integrity Under Stress
Impact Resistance and Long-Term Performance
PU panels stay strong even when hit or stressed. Tests show the glue between layers helps them handle impacts. Panels with denser foam cores, like 80 kg/m³, hold up to 1261.48 N, which is 41.7% better than less dense ones.
They soak up impact energy, lowering the chance of breaking.
The strong glue keeps layers together, making them last longer.
These qualities make PU panels a solid choice for strength and long-term use.
Durability Factors
Resistance to Environmental Factors
Moisture and Water Resistance
PU sandwich panels are great at keeping out water. The foam core blocks moisture from reaching the inner layers. This helps the panels stay strong, even in wet places. Using the right materials makes them even better at resisting water damage.
Environmental Factor | Effect on PU Sandwich Panels |
---|---|
Humidity | Weakens glue, causing layers to come apart. |
Moisture | Foam stops water, protecting the inside layers. |
Thermal Stability in Extreme Temperatures
PU panels work well in very hot or cold weather. The foam and metal layers stop the panels from expanding or shrinking. This keeps them strong and in shape for a long time. Picking the right materials helps them handle extreme temperatures better.
Environmental Factor | Effect on PU Sandwich Panels |
---|---|
Extreme Heat | Makes the panel expand. |
Extreme Cold | Makes the panel shrink. |
Thermal Extremes | Good materials stop heat or cold from causing changes. |
Corrosion Resistance
Protection Against Rust and Degradation
The metal layers of PU panels resist rust and damage. Special coatings protect the metal from corrosion in tough conditions. This keeps the panels strong and looking good for years. They are reliable in places with moisture or chemicals.
Longevity and Maintenance
Lifespan of 20-50 Years with Proper Care
PU panels can last 20 to 50 years if cared for well. Their strong design and resistance to damage make them last longer. Regular checks and small fixes can help them stay useful for decades.
Low Maintenance Requirements
These panels are easy to take care of. They resist water, rust, and temperature changes, so they don’t need many repairs. Simple care keeps them in great shape with little effort.
Applications and Performance
Construction Industry
Use in Walls, Roofs, and Floors
PU sandwich panels are used in building walls, roofs, and floors. They are light, making them easy to install. Their strength helps them hold heavy weights safely. These panels also keep buildings warm in winter and cool in summer. For example, a New York building saved 30% on heating and cooling costs by using PU panels. This shows how they help save energy and money.
Performance in Residential and Commercial Buildings
PU panels work well in homes and businesses. They last long because they resist water, weather, and wear. These panels make buildings stronger and need less fixing over time. They also keep temperatures steady, saving energy and making spaces more comfortable.
Refrigeration and Cold Storage
Thermal Insulation Properties
PU panels are great for cold storage because they block heat.
The foam core keeps temperatures steady inside.
They use less energy, helping food and medicine industries.
Strong outer layers make them durable and fire-resistant.
Durability in Low-Temperature Environments
These panels work well in freezing places.
They stop water damage in cold conditions.
Their insulation makes refrigeration more efficient.
Known worldwide, they improve energy use in cold storage.
Other Applications
Transportation and Automotive
PU panels are key for cold transport. They keep food and medicine cold during trips. This makes them important for delivery services needing temperature control.
Industrial Uses
Factories and warehouses use PU panels for energy savings. They keep temperatures steady, helping industries like e-commerce. Their light design is easy to install and lowers energy costs, making them a top choice for many uses.
Comparison with Alternatives
PU Sandwich Panels vs. EPS Panels
Strength and Load-Bearing Comparison
PU panels are much stronger than EPS panels. Their rigid foam core and strong layers handle heavy loads well. This makes them great for tough jobs needing durability. EPS panels are lighter but not as strong. Their foam core squishes easily, so they can’t handle much stress.
PU panels absorb 21% more energy in bending tests.
Their closed-cell foam resists bending and stays strong longer.
EPS panels work for light tasks but fail in tough conditions.
Durability in Harsh Environments
PU panels last longer in bad weather. Their foam core blocks water, and metal layers protect them in wet places. EPS panels soak up water, which weakens them over time. PU panels also handle heat and cold better, keeping their shape and strength.
PU Sandwich Panels vs. Mineral Wool Panels
Thermal and Moisture Resistance
PU panels keep heat out better than mineral wool panels. Their foam core saves energy by reducing heating and cooling costs. Mineral wool works well in hot places but doesn’t block water like PU panels. PU’s closed-cell foam stops water from getting in, making it great for humid areas.
PU panels cut emissions by improving insulation.
Mineral wool is strong but doesn’t handle moisture as well.
Longevity and Maintenance
PU panels need less care than mineral wool panels. Their strong glue and rust-proof metal last up to 50 years with little upkeep. Mineral wool panels are durable but need more checks because of water issues.
Cost-Effectiveness and Performance Balance
Value for Money
PU panels are affordable and work well. They cost less to install than honeycomb panels, which need special tools. PU panels also save money by cutting energy use with better insulation.
Suitability for Different Applications
PU panels work in many areas, like buildings and cold storage. They are strong and last long, making them good for walls, roofs, and floors. They also keep things cold during transport, staying reliable over time.
PU panels are strong, durable, and a smart choice for many uses.
PU sandwich panels are strong and long-lasting, making them useful in many industries. Their foam core keeps heat out, saving energy in cold storage and transport. These panels help keep temperatures steady, which is great for storing food and medicine. They are light, making building easier and reducing weight on structures. They also resist mold, mildew, and rot, working well in tough conditions. With less upkeep and lower energy bills, PU panels are a smart and cost-effective choice.
If you need tough, energy-saving materials, PU panels are a great option.
FAQ
What are PU sandwich panels made of?
PU sandwich panels have a foam core and two metal layers. The foam, made of polyurethane, keeps heat out and adds strength. The metal layers, often steel or aluminum, protect and make them last longer. Together, they form a light but strong panel.
How long do PU sandwich panels last?
PU sandwich panels can last 20 to 50 years with care. The strong glue, rust-proof metal, and water-blocking foam keep them durable. Checking them often can help them stay in good shape for a long time.
Are PU sandwich panels energy-efficient?
Yes, PU sandwich panels save energy well. The foam core keeps heat in or out, lowering heating and cooling costs. This makes them great for cold storage, fridges, and energy-saving buildings.
Can PU sandwich panels resist water damage?
PU sandwich panels block water very well. The foam stops moisture, and the metal layers keep water out. This makes them good for wet places or areas with high humidity.
Where can you use PU sandwich panels?
PU sandwich panels are useful in many places. They work for walls, roofs, and floors in buildings. They are also great for cold storage, trucks, and factories needing insulation. Their many uses make them a top choice in different industries.