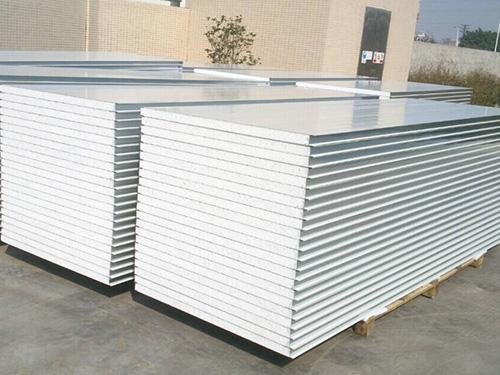
Sandwich panels are modern building materials designed with specific Sandwich Panel Specifications for enhanced strength. They assist with energy absorption and bending in structures, outperforming solid sheets by absorbing more energy, which makes them ideal for projects involving moving forces. Understanding the Sandwich Panel Specifications is crucial for ensuring their effective performance in any project.
Key Takeaways
Sandwich panels are light but strong, perfect for building projects needing energy savings and toughness.
Picking the right core material is key for insulation and strength; choices include foam, mineral wool, and polystyrene.
Always review the panel’s details, like thickness and surface materials, to make sure they fit your project needs.
What Are Sandwich Panels?
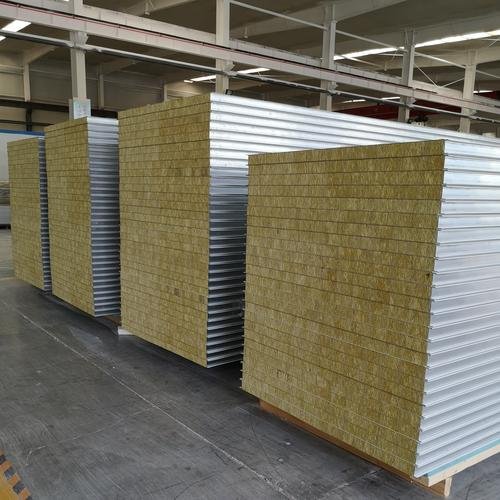
Structure and Components
A sandwich panel is made of three main layers. The middle layer, called the core, is light but strong. It is often made from materials like PIR (polyisocyanurate), mineral wool, or XPS (extruded polystyrene). This core is placed between two thin, hard outer layers. These outer layers are usually made of metal, fiberglass, or plastic. Together, these layers make a material that is light and very strong.
The design of sandwich panels works like an I-beam. The outer layers handle bending, while the core resists cutting forces and adds thickness without much weight. This makes sandwich panels strong and stiff, perfect for projects needing strength and efficiency.
Core Materials: Foam, honeycomb, or other light materials.
Face Materials: Metal, plastic, or fiberglass.
Key Features: Light, strong, and stiff.
Purpose and Benefits
Sandwich panels are used in many industries for different purposes. Their main job is to give support while also offering benefits like insulation and strength. For example, they keep heat in or out, so you don’t need extra insulation. This saves energy and money.
Benefit/Application | Description |
---|---|
Thermal Efficiency | Keeps heat in or out with great insulating materials. |
Energy Efficiency | Saves money by lowering heating and cooling costs. |
Soundproofing | Helps reduce noise in busy or loud places. |
Durability | Stands up to tough weather, wind, and water. |
Ease of Installation | Light design makes building faster and cheaper. |
You can see sandwich panels in offices, homes, and even temporary buildings. They are popular because they are useful and save time and energy in construction.
Tip: Always check your project needs before choosing sandwich panels for the best results.
Applications of Sandwich Panels
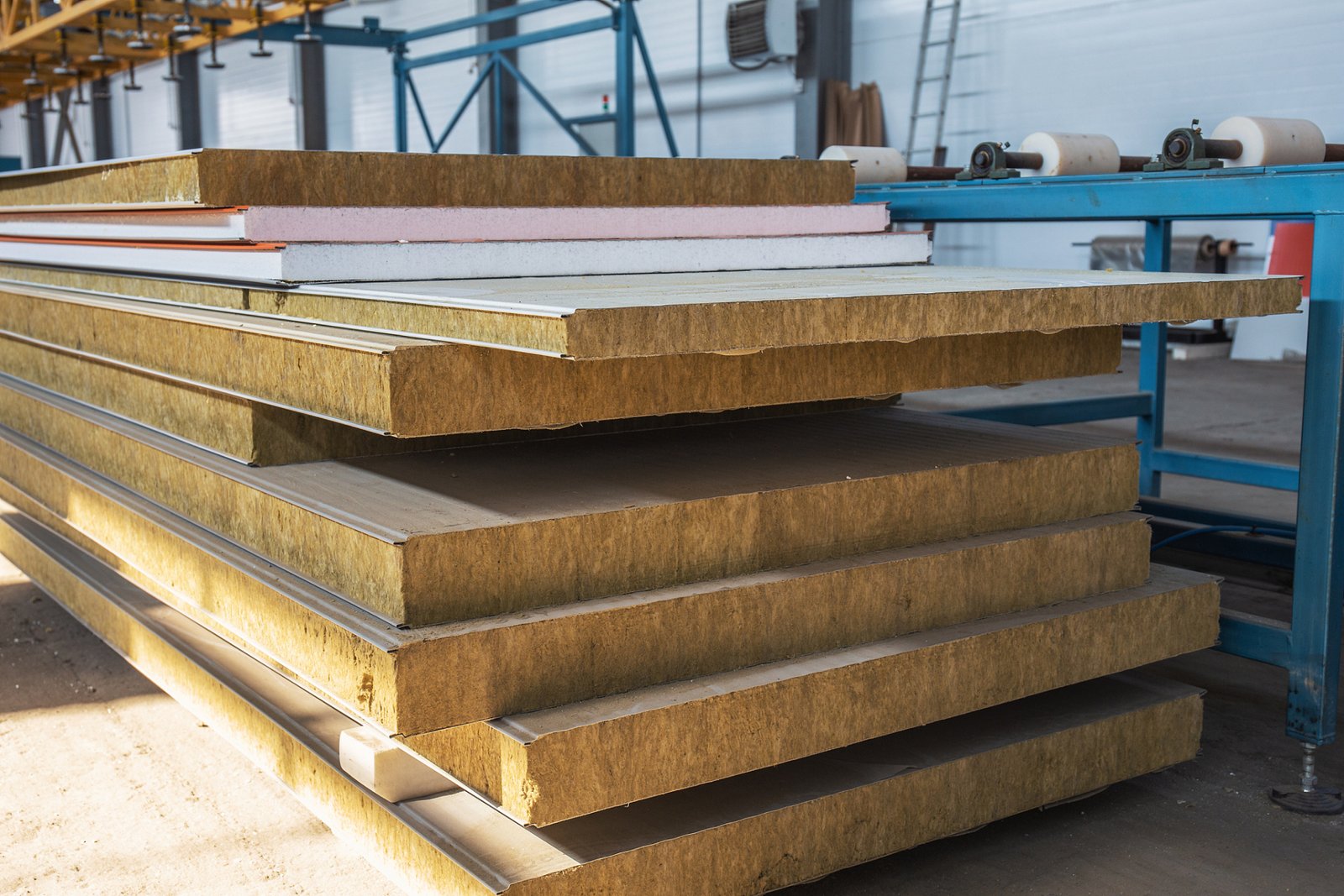
Industrial and Commercial Use
Sandwich panels are important in industrial and commercial buildings. They are often used for walls and roofs because they are strong and weatherproof. These panels help save energy by keeping buildings warm or cool. Factories, warehouses, and malls use them for their strength and easy setup.
The Sandwich Panels Market was worth $9.95 billion in 2023. It may grow to $20.39 billion by 2032, with an 8.3% yearly growth rate.
More industries are using these panels to save money and be eco-friendly.
Residential Construction
In homes, sandwich panels are used for walls, roofs, and floors. They are light, so moving and installing them is simple. This saves time and money. They also keep homes warm in winter and cool in summer. Their soundproofing helps block noise, which is great for city homes.
Cold Storage and Refrigeration
Sandwich panels are key for cold storage and refrigeration. They keep spaces cold, which is vital for food and medicine industries. These panels help save energy and lower costs. In 2020, the U.S. had about 1.25 billion cubic feet of cold storage, showing the need for these panels.
Specialized Applications
Sandwich panels are also used in special ways. Hospitals and labs use them for clean rooms because they are easy to clean. Modular buildings, like temporary offices, use them for quick setup. Refrigerated trucks use them to keep goods cold during travel.
Sandwich panels are useful in many industries. Knowing their uses helps you pick the right one for your needs.
Types of Sandwich Panels
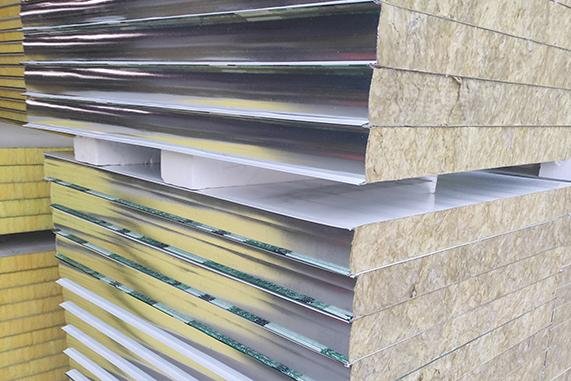
Wall Panels
Wall panels work well for inside and outside walls. They make strong, insulated walls that handle weather changes. The core, like polyurethane or mineral wool, keeps heat in or out. The outer layers, usually steel or aluminum, protect from damage and weather. These panels are simple to install and are used in homes, offices, and factories.
Tip: Pick wall panels with the right core for better insulation.
Roofing Panels
Roofing panels protect buildings and save energy. They are light but strong, perfect for big roofs in factories, warehouses, or homes. The core, such as PIR or EPS, keeps temperatures steady. The outer layers block rain, wind, and sunlight. Many roofing panels have locking systems for a tight, weatherproof fit.
Acoustic Panels
Acoustic panels help reduce noise in busy places. They are great for offices, theaters, and factories. The core and design decide how well they block sound. For example, vacuum or honeycomb cores reduce noise better than regular panels, especially between 100-2000 Hz.
Test Condition | Result |
---|---|
New sandwich structures | Block more sound than regular panels up to 1800 Hz |
Frequency analysis | Great noise reduction in important sound ranges |
These panels are ideal for spaces needing quiet environments.
Fire-Resistant Panels
Fire-resistant panels keep buildings safe during fires. They use non-burning cores like mineral wool that handle high heat. These panels meet strict safety rules, like ISO 13784-1 and EN 13501-1. For example, the ISO 13784-1 test uses a propane burner to check fire resistance over 20 minutes. This ensures they protect well in emergencies.
Note: Always check fire safety labels to follow local building rules.
Sandwich Panel Specifications and Standard Sizes
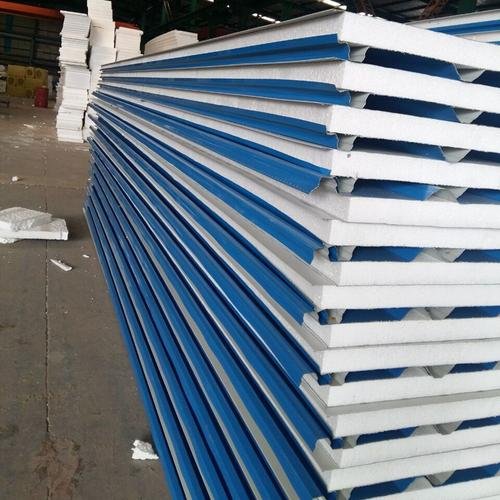
Common Thicknesses
The thickness of sandwich panels is very important. Most panels are between 40 mm and 200 mm thick. Thicker panels are used for cold storage to keep things insulated. Thinner panels, like 40–50 mm, work well for home walls. Some lightweight panels are even thinner, like 15 mm or 20 mm.
Thicker panels block heat and sound better. They are great for saving energy or reducing noise. Always pick the right thickness for your project to get the best results.
Standard Widths
Sandwich panels usually have standard widths for easy use. Most are 1,000 mm wide, but some are 1,150 mm. These sizes work for many projects, like factories or homes. Standard widths also make building faster and reduce waste.
Length Options
Panels come in different lengths to fit building needs. Common lengths are 3 to 6 meters. Some panels can be as long as 16 meters for big projects. Guides like “Design & Engineering with Wall Panels” suggest choosing lengths based on your building plans. Long panels are good for factories, while short ones are better for homes.
Variations by Application
Sandwich panels are made for different jobs. Fire-resistant panels meet strict safety rules like Euroclasse 13501-1. Soundproof panels focus on blocking noise. Panels for cold storage keep temperatures steady with special thermal properties. Knowing these differences helps you pick the right panel for your project.
Tip: Always check the panel’s technical sheet to match your project needs.
Key Specifications to Consider
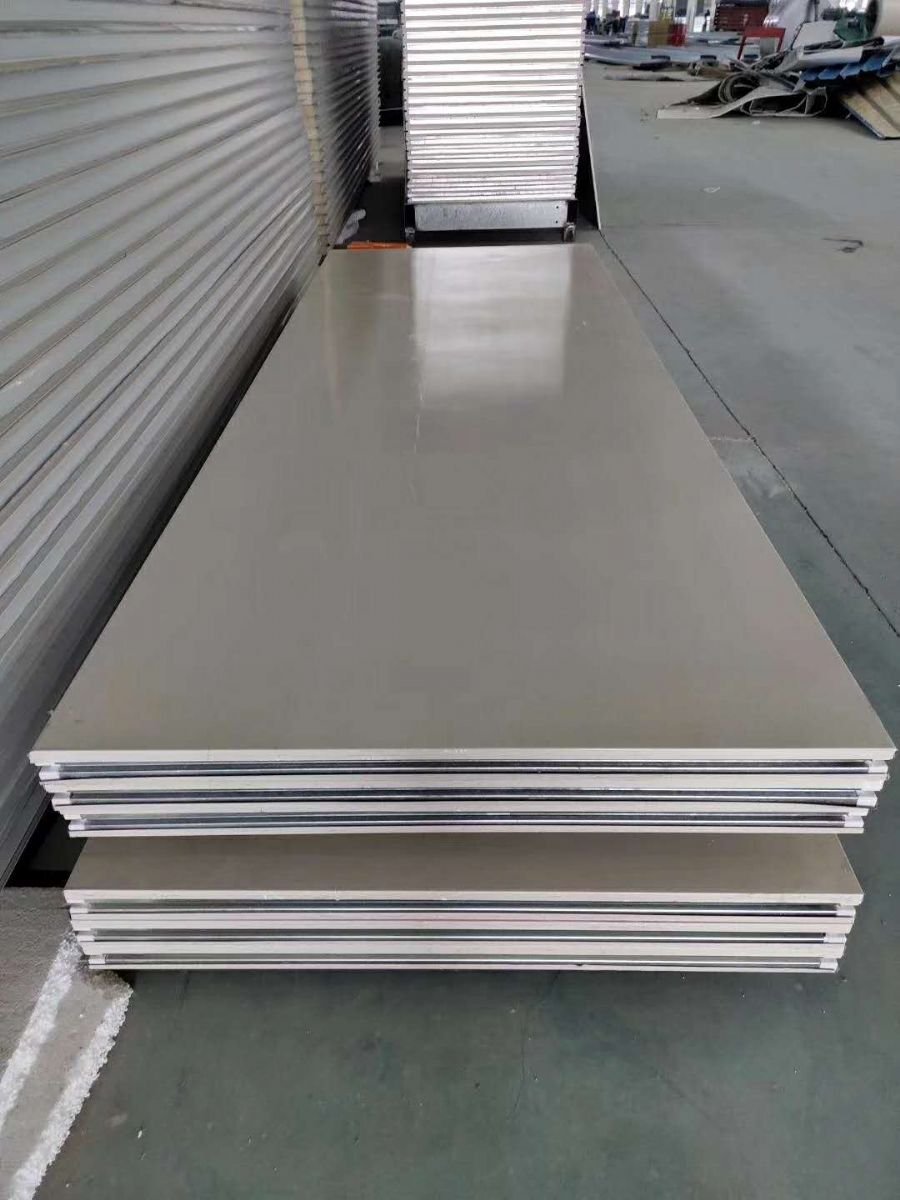
Core Materials
The core material is the most important part of a sandwich panel. It decides how strong, insulated, and energy-absorbing the panel is. Common core materials include polyurethane (PU), polyisocyanurate (PIR), mineral wool, and extruded polystyrene (XPS). Each material has its own strengths. For instance, PIR gives great thermal insulation, while mineral wool is excellent for fire safety.
Studies show that the core’s design affects how it works. Panels with cubic patterns absorb more energy and handle stronger impacts. This makes them perfect for projects needing strength and safety. When picking a core material, think about your project’s insulation, fire safety, and strength needs.
Facing Materials
The outer layers, called facings, protect the core and add strength. These layers are usually made of steel, aluminum, or fiberglass. Steel is tough and resists weather damage. Aluminum is light and doesn’t rust. Fiberglass is flexible and used for special purposes.
The right facing material depends on the location. For example, steel is great for factories, while aluminum works well near the sea because it resists saltwater. Always choose a facing material that fits your project’s environment for the best results.
Locking Systems
Locking systems help panels fit tightly together. This improves strength and keeps out weather. Common systems include tongue-and-groove and cam-lock designs. Tongue-and-groove is easy to install and looks smooth. Cam-lock systems are stronger and work well for cold storage or high-pressure areas.
Tests, like those in the Chinese Standard for concrete structures (GB/T50152-2012), check how locking systems perform under stress. These tests help you pick the right system for your project’s needs.
Coatings and Finishes
Coatings and finishes protect panels from damage and make them look better. Popular coatings include polyester, PVDF (polyvinylidene fluoride), and epoxy. Polyester is cheap and good for indoor use. PVDF resists UV rays, so it’s great for outdoor use. Epoxy is strong against chemicals, making it ideal for factories.
Finishes also affect how panels look. Smooth, textured, or embossed finishes can match your style. Always check if the coating is durable and fits your environment for long-lasting use.
Tip: Always read the technical sheet to ensure the panel meets your project’s needs.
Choosing the Right Sandwich Panel
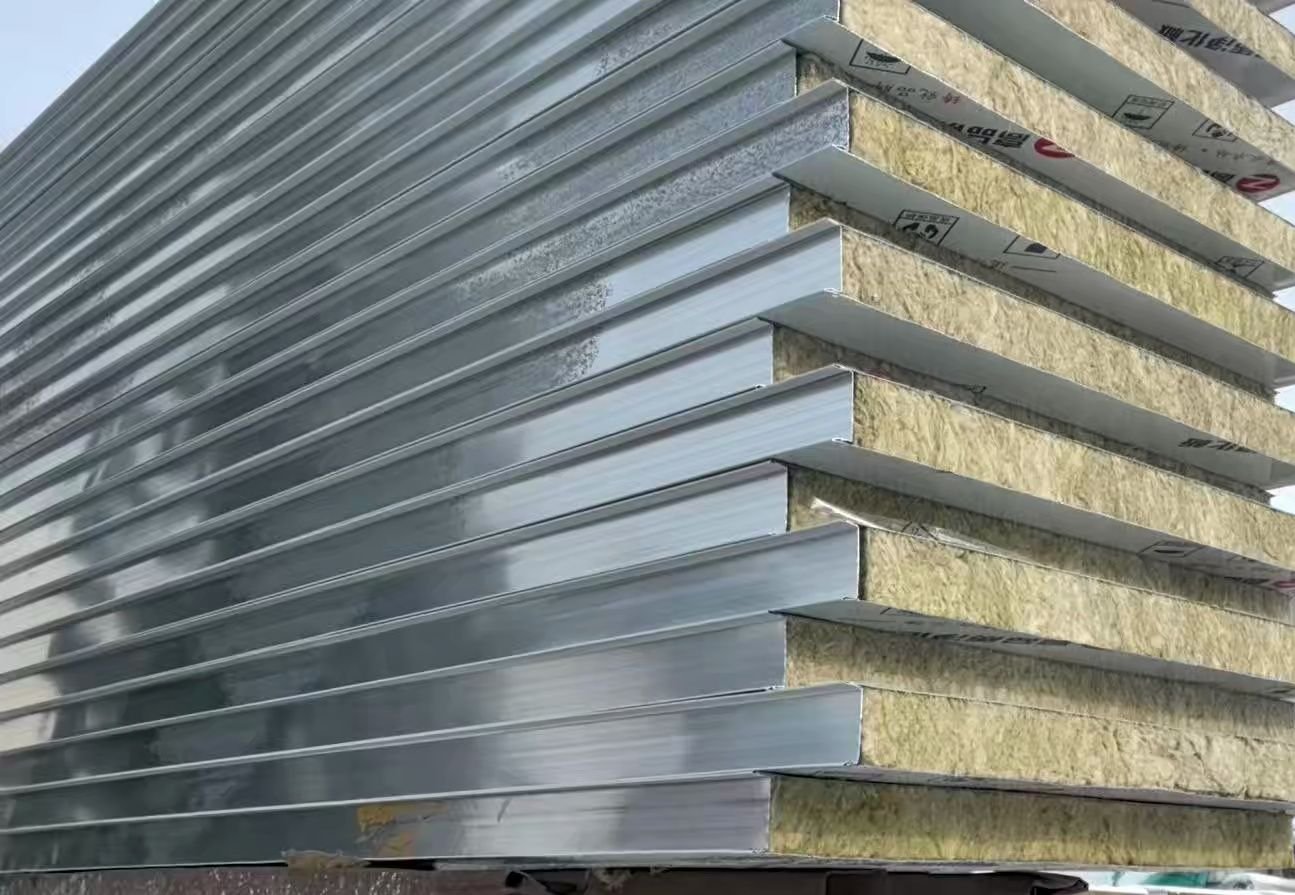
Application Needs
Picking the right sandwich panel starts with knowing your project. Different jobs need specific features. For example, cold storage needs great thermal insulation. Industrial buildings may need panels that resist fire. Think about these factors when choosing:
Fire resistance for safety in risky areas.
Sound insulation properties to reduce noise in quiet spaces.
Panel thickness for proper insulation and strength.
Type of filler for better thermal or sound performance.
Weight to match your building’s structure.
Climatic conditions to handle local weather.
Tip: Look at examples like “Sandwich Panel Design Criteria” to learn how panels work for different needs.
Case Study Reference | Description |
---|---|
Sandwich Panel Design Criteria | Shows how panels meet various project needs effectively. |
Environmental Conditions
Your location affects which panel you should pick. Coastal areas need aluminum facings to stop rust. Places with very hot or cold weather need panels with strong insulation. In humid areas, panels should resist moisture to last longer. Always choose materials and coatings that fit your area for better durability.
Technical Details
Technical details show how well a panel works. Focus on these:
Thermal insulation properties to save energy.
Fire resistance to meet safety rules.
Mechanical strength for strong structures.
Each detail affects how the panel performs. Thicker panels with dense cores insulate and support better. Always check the technical sheet to ensure the panel fits your project.
Installation Tips
Easy installation saves time and money. Lightweight panels are simpler to move and install. Locking systems like tongue-and-groove or cam-lock make a tight fit. This improves strength and stops gaps that let in moisture or air. Pick panels made for easy setup to speed up construction.
Note: Work with experts to ensure the panels are installed correctly for the best results.
Advantages and Drawbacks
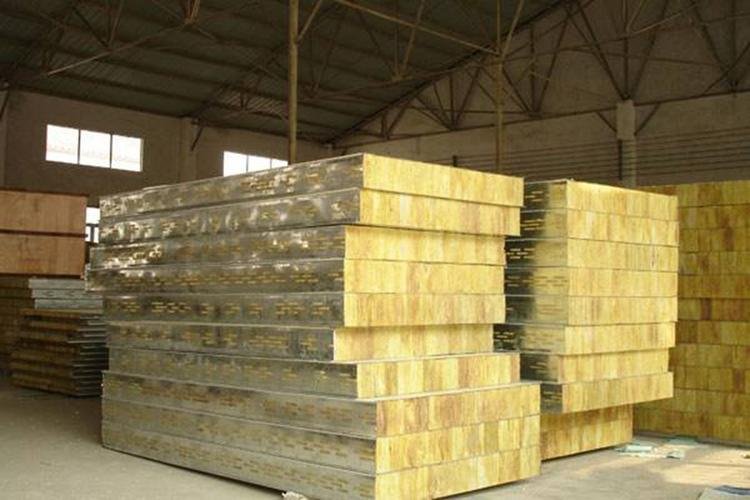
Benefits of Sandwich Panels
Sandwich panels have many benefits for construction projects. They are light, which lowers the weight on buildings. This makes moving and setting them up faster and cheaper. Using structural insulated panels (SIPs) can cut labor costs by 55%. They also help finish construction quicker, especially for walls and roofs.
These panels are very strong. They resist bending and handle heavy loads well. Their strength makes them last longer in different uses. The table below shows how they perform:
Metric | Result |
---|---|
Bending Stiffness | Strong in both directions |
Maximum Bending Moment | Strong in both directions |
Compression Strength | Matches bending strength |
Screw Resistance | Matches bending strength |
Dowel Bearing | Better with fiber-made panels |
Sandwich panels also save energy. They keep indoor spaces warm or cool, cutting heating and cooling costs. Panels with the right fiber setup can absorb 72.18% more energy and handle 46.9% more force. These features make them great for projects needing strength, insulation, and savings.
Limitations and Challenges
Sandwich panels do have some downsides. One problem is they can get damaged by slow impacts. A study called Low-Velocity Impact Damage Quantification on Sandwich Panels by Thermographic and Ultrasonic Procedures explains this. It says that while panels are strong, finding damage needs special tools like thermographic or ultrasonic tests. Regular checks might miss some problems, which could be unsafe.
Weather can also affect these panels. Extreme heat, cold, or moisture can wear them out if they don’t have the right coating. Picking good materials and finishes helps them last longer in tough conditions.
Lastly, sandwich panels can cost more upfront than regular materials. But they save money over time with lower energy and labor costs. By thinking about your project needs, you can decide if these panels are the best choice.
Tip: Check your panels often and fix issues early to make them last longer.
Knowing about sandwich panel specifications and sizes helps you choose wisely. Picking the correct panel improves insulation, strength, and energy savings.
Key Takeaway: Always pick panels that fit your project’s needs. Choosing well ensures they last longer and save money over time.
FAQ
How long do sandwich panels last?
Sandwich panels can last 20 to 50 years. Their durability depends on the materials, coatings, and weather. Taking care of them helps them stay strong and useful.
Are sandwich panels recyclable?
Yes, many sandwich panels can be recycled. Materials like steel, aluminum, and some cores can be reused. Check with your local recycling center for rules.
How should you care for sandwich panels?
Wash panels with mild soap and water often. Look for any damage or rust. Fix small problems quickly to keep them lasting longer.