
Picking the right sandwich panel is very important. These panels help keep temperatures steady to protect food and medicine. In 2023, the global market for cold storage panels was worth $1.8 billion. It is expected to grow by 6.7% yearly, reaching $3.2 billion by 2032. This shows more people need better cold storage solutions. New insulation materials like polyurethane save energy, cut costs, and work better. They are a must-have for places needing controlled temperatures.
Key Takeaways
Picking the right sandwich panel keeps cold storage temperatures steady. This protects items like food and medicine from spoiling.
Panels made of polyurethane or polyisocyanurate keep heat out well. They save energy and lower costs in cold storage systems.
Checking and fixing sandwich panels often helps find damage early. This keeps cold rooms clean and working for a long time.
Modular sandwich panels are easy to move and set up. They are great for portable cold storage when businesses need changes.
Good sandwich panels save energy, last longer, and stay safe. They help cold storage systems work better and succeed.
Understanding Sandwich Panels in Cold Chain Logistics
What Is a Sandwich Panel?
A sandwich panel is a building material that provides insulation and support. It has two outer layers, usually steel or aluminum, with an insulating core. The core materials can be polyurethane, polystyrene, or mineral wool. These panels are strong but lightweight, perfect for cold rooms and fridges.
Aspect | Details |
---|---|
Definition | |
Core Materials | Includes polyurethane, polystyrene, and mineral wool. |
Skin Materials | Steel and aluminum are common, each offering unique benefits. |
Applications | Used in cold storage, transport, and industrial buildings. |
The Role of Sandwich Panels in Cold Room Applications
Sandwich panels help cold rooms work better by stopping heat transfer. They keep the inside temperature steady, protecting food and medicine. These panels also save energy by improving fridge system efficiency.
New materials like polyurethane foam make these panels insulate even better. This keeps temperatures stable, even in tough conditions.
Benefits of Using Sandwich Panels in Cold Chain Logistics
Using sandwich panels in cold chain logistics has many benefits:
Energy Efficiency: Great insulation lowers energy bills.
Durability: Strong materials last a long time.
Hygiene: Smooth surfaces are easy to clean, ideal for food and medicine.
Versatility: Modular designs make them easy to move and set up.
Characteristic/Function | Description |
---|---|
Materials Used | Polyisocyanurate and phenolic foam for fire safety and thermal stability. |
Applications | Used for storing food, medicine, chemicals, flowers, and electronics. |
Market Trends | More demand for cold storage due to sensitive products. |
End-Users | Warehouses, stores, and specialized facilities. |
Opportunities | Growth in online shopping and better insulation materials. |
Choosing the right sandwich panel saves money and keeps products safe. These panels are key to running cold storage and packaging systems effectively.
Types of Sandwich Panels for Cold Chain Applications

Refrigeration Sandwich Panels
Refrigeration panels help keep cold rooms at low temperatures. They use strong insulation materials like polyurethane (PUR) or polyisocyanurate (PIR). These materials control temperatures well, from 32°F to -13°F. This makes them perfect for storing food, medicine, and chemicals.
The insulation in these panels stops heat from entering. This keeps the inside temperature steady and saves energy. PIR panels are great for fire safety and work well in risky places like chemical storage. Phenolic foam panels are also safe, with low smoke and high thermal efficiency.
Tip: Use insulated doors with refrigeration panels to save more energy.
Roof and Wall Sandwich Panels
Roof and wall panels are important for cold storage buildings. They provide insulation and support, making cold rooms strong and efficient. Rigid polyurethane foam is often used to stop cold air from escaping.
Modern cold storage uses insulated metal panels for roofs and walls. These panels keep the inside cold and protect against outside weather. Mineral wool panels are fireproof and reduce noise, which is helpful in cities.
Note: Roof panels block heat from sunlight, improving energy savings.
Modular Sandwich Panels for Portable Cold Rooms
Modular panels are great for portable cold rooms. They are pre-made, so they are quick to set up. Businesses can install them fast, saving time and starting use right away. This is useful for temporary or flexible storage needs.
These panels are light, making them easy to move and install. They also insulate well, keeping temperatures steady in tough conditions. For example, modular rooms with PIR or PUR panels protect stored items effectively.
Tip: Modular cold rooms are easy to move and reuse for changing needs.
Specialty Sandwich Panels for Tough Conditions
For tough conditions, special sandwich panels are needed. These panels work well in cold rooms in harsh places. They keep insulation steady and stay strong, even in hard situations.
These panels use advanced materials like PIR or mineral wool. PIR works well in freezing cold, while mineral wool is fireproof. This makes them great for storing vaccines or chemicals safely.
Manufacturers test these panels to ensure they work well. Common tests include:
Test Method | What It Checks |
---|---|
ASTM D 1781 | Checks how well the layers stick together. |
ASTM C 393 | Tests strength, stiffness, and bonding under pressure. |
ASTM C 297 | Measures how strong the panel is through its thickness. |
ASTM C 364 | Checks how much pressure the panel can handle. |
These tests prove the panels can handle tough conditions. For example, in deserts, the outside is hot, but the inside stays freezing. These panels stop heat from getting in, keeping items safe.
The outer layers of the panels also matter. Steel or aluminum with coatings stops rust and damage. This makes the panels last longer, even in wet or rough weather.
Picking the right panel helps control temperatures and protect your goods, even in the hardest places.
Key Factors for Picking the Best Sandwich Panel
Insulation Properties
Keeping Heat Out with R-Value
When choosing a sandwich panel, insulation is very important. The R-value shows how well a material blocks heat. A higher R-value means better insulation and steady cold room temperatures. Materials like polyurethane (PUR) and polyisocyanurate (PIR) are great insulators. They are often used in cold storage to keep spaces cool and energy-efficient.
Insulation Material | Thermal Conductivity (W/m·K) | Common Uses |
---|---|---|
Polyurethane (PUR) | Cold storage, food factories, industrial | |
Polyisocyanurate (PIR) | 0.020-0.026 | Cold storage, food factories, industrial |
Good insulation saves energy and lowers cooling costs. This makes it essential for cold chain systems.
Blocking Moisture and Vapor
Stopping moisture is also very important for cold rooms. Panels that block water, steam, and air stop condensation. This protects stored items and keeps the insulation working well. For medicine storage, moisture-proof panels are necessary to maintain cleanliness.
Core Materials
Polyurethane (PU) and Polyisocyanurate (PIR)
Polyurethane insulates well and is popular for cold panels. But it doesn’t resist fire. Polyisocyanurate is better because it forms a protective layer in fire. PIR panels are also strong and light, making them easy to install.
Expanded Polystyrene (EPS)
EPS is a cheaper option and insulates well for some uses. However, it doesn’t resist fire as well as PIR or mineral wool. EPS is often used in roofs and walls where fire safety isn’t a big concern.
Mineral Wool
Mineral wool is great for fire safety and soundproofing. It works well in places like airports and malls. It insulates walls and keeps buildings strong, making it a flexible choice.
Facing Materials
Steel and Aluminum Layers
The outside of panels is usually steel or aluminum. Steel is strong, while aluminum is light and doesn’t rust. Both materials keep panels sturdy and long-lasting.
Coatings for Extra Protection
Special coatings make the outer layers last longer. These coatings stop rust and damage, even in tough conditions. For cold storage, coated panels add extra protection from wear and tear.
Technical Specifications
Fire Resistance Standards
Fire resistance shows how well panels handle fire safely. It checks if panels stay strong during a fire. This is very important for places storing food or medicine. Mineral wool cores stop fires from spreading quickly. They slow down big fires, making them great for busy areas like malls or airports.
Materials must also perform well when touched by flames. Panels with mineral wool cores follow strict fire safety rules. These rules check if panels stay stable, sealed, and insulated during fires. Fire tests also look at how materials react to heat or flames. These tests make sure panels protect cold rooms and stored items during emergencies.
Load-Bearing and Structural Integrity
Sandwich panels must hold weight without breaking or bending. Steel outer layers make them strong, while light cores like PIR are easy to build with. Together, they help panels work well in cold storage systems.
The middle layer is key for insulation, fire safety, and noise control. Mineral wool cores insulate well and meet fire safety rules. This makes them good for cold rooms in factories or stores. Always pick panels that can handle the weight your system needs.
Panel Thickness for Different Applications
Thicker panels insulate better and keep temperatures steady. This is important for cold rooms storing sensitive items like medicine. Thick panels stop temperature changes and keep items safe.
The right thickness depends on the type of cold room. For example, walk-in freezers need thicker panels than regular fridges. Ask experts to help you choose the right thickness. This saves energy and makes panels last longer.
Installation and Maintenance of Sandwich Panels
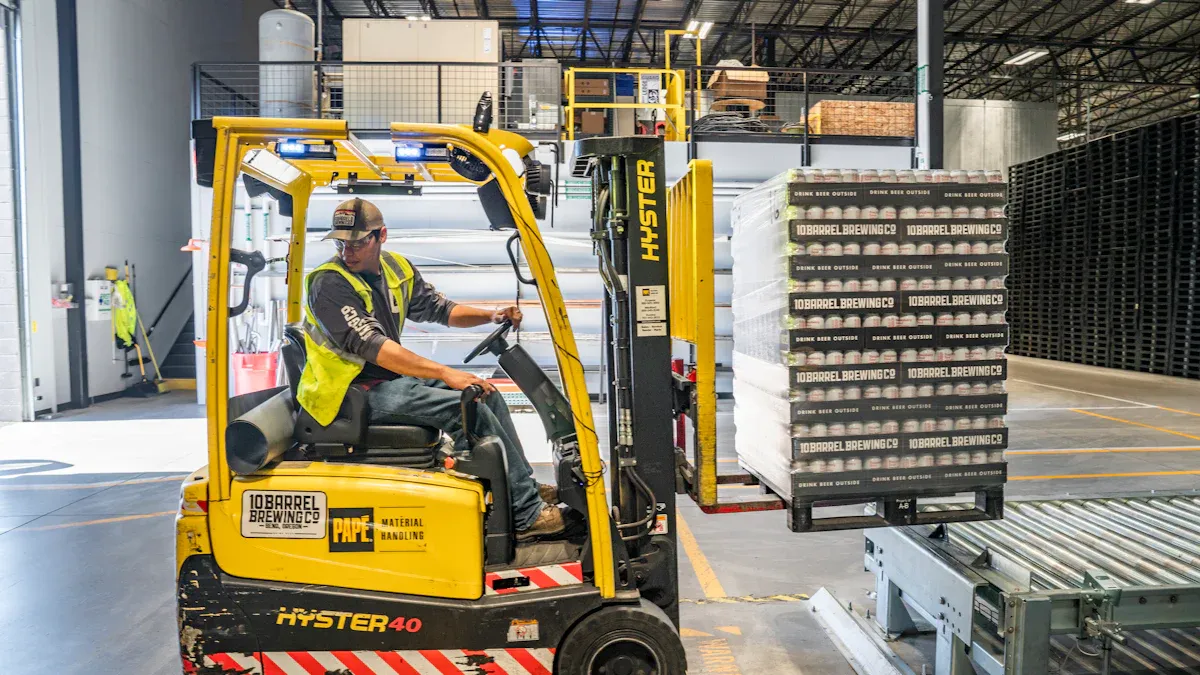
Best Practices for Installation
Keeping Cold Rooms Airtight
Airtight seals are very important for cold room efficiency. They stop air leaks that raise energy costs and harm cooling. Use good sealants to close gaps between panels tightly. Check all joints during setup to ensure no spaces are left.
Fasteners also help keep panels sealed and strong. Interlocking fasteners improve insulation and hold panels firmly. Follow the manufacturer’s instructions for joining panels correctly. This ensures the best results for your cold room.
Key Aspect | Details |
---|---|
Sealing stops air leaks and keeps rooms efficient. | |
Use quality sealants and check all panel joints. | |
Fixing Systems | Includes visible, hidden, and interlocking fasteners. |
Benefits of Fixing Systems | Interlocking fasteners improve strength and insulation. |
Stopping Heat Leaks During Setup
Heat leaks, or thermal bridges, happen in poorly insulated spots. These weaken the cold room’s insulation and waste energy. To prevent this, make sure panels fit tightly with no gaps. Use insulation materials that match the panel type.
Install panels in the right order: floor first, then walls, and ceiling last. This reduces the chance of heat leaks. Always seal the panel edges properly to block heat from entering.
Maintenance Tips for Longer Use
Checking for Damage Often
Regular checks help find and fix problems early. Look for dents, cracks, or loose parts in the panels. Damaged panels can lower insulation and hurt cooling performance. Keep a log of inspections to track repairs and maintenance.
Cleaning for Hygiene
Clean your cold room often to keep it safe and hygienic. Follow cleaning instructions from the manufacturer. Use soft materials to avoid scratching the panels. Proper cleaning helps panels last longer and keeps food storage safe.
Tip: Train workers on cleaning and handling to avoid damage.
Upgrading Panels for New Needs
Your business needs may change as it grows. Upgrading panels can help meet these new requirements. For example, thicker panels can improve insulation, and fire-resistant ones add safety. Talk to experts to pick the right upgrades for your cold room.
Note: Upgrades can save energy and improve cooling over time.
Picking the right sandwich panel is very important for cold storage. It helps keep temperatures steady to protect delicate items. The correct panel also saves energy, lasts longer, and works better. Think about your needs and ask experts for advice. This way, your products stay safe, and your business succeeds in cold chain logistics.
FAQ
What matters most when picking a sandwich panel for a cold room?
The insulation is the most important part. Panels with good insulation and moisture protection keep temperatures steady. This saves energy and keeps products safe.
How can you keep sandwich panels in good shape?
Check panels often for cracks or dents. Clean them gently to avoid scratches. Follow the maker’s care tips to keep them strong and clean.
Can sandwich panels in a cold room be upgraded?
Yes, you can upgrade panels to fit new needs. Thicker panels insulate better, and fire-safe ones add protection. Ask experts to help pick the best upgrades.
Are modular sandwich panels good for portable cold rooms?
Yes, modular panels are great for portable cold rooms. They are light, easy to set up, and insulate well. These are perfect for businesses needing quick or temporary storage.
What materials are used in sandwich panels?
The core is often made of polyurethane, polyisocyanurate, or mineral wool. The outside layers are usually steel or aluminum for strength and durability.