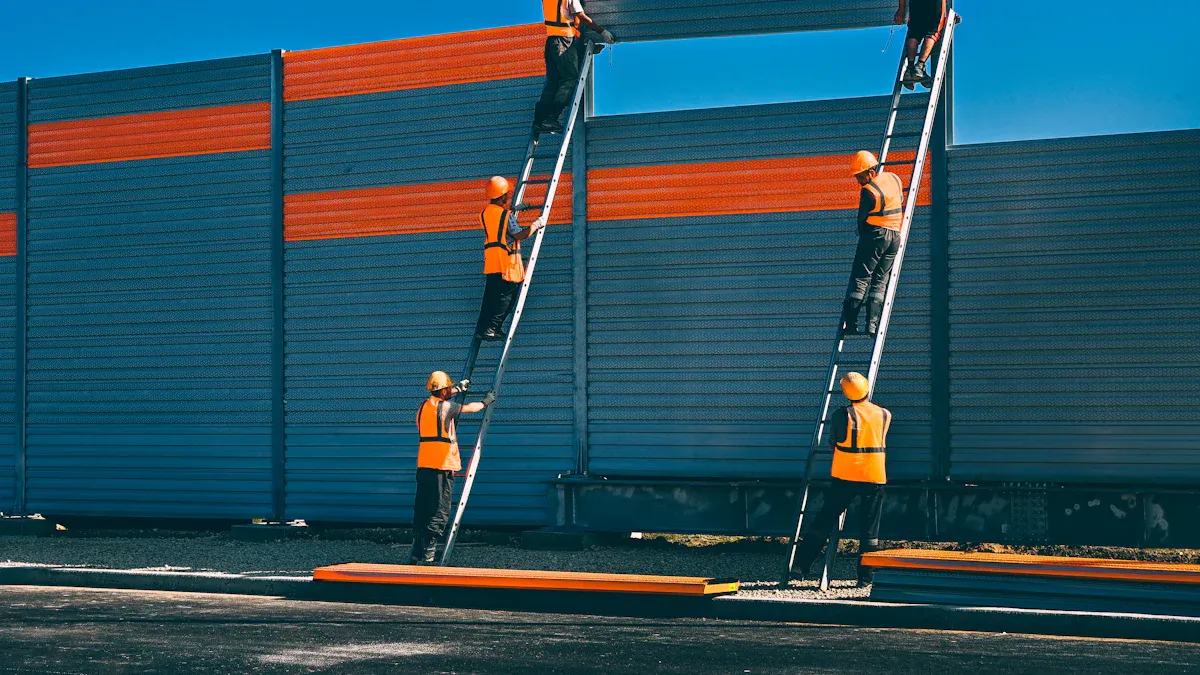
Explosion-proof buildings are made to handle explosion forces safely. They protect people and places in dangerous areas. These buildings lessen blast effects, reducing harm and keeping people safe. For instance, concrete blast panels can cut movement by 22% and lower speed by 86%. Sandwich panels are very important in these buildings. Their special design helps block shockwaves and soak up energy. This makes them key in today’s building plans. As safety becomes more important worldwide, the explosion-proof building market is expected to grow a lot. This shows the need for strong and smart building ideas.
Key Takeaways
Explosion-proof buildings keep people and property safe from blasts.
Sandwich panels are important because they absorb energy and lower damage.
Advanced materials like aluminum foam make sandwich panels safer and stronger.
Sandwich panels are affordable and long-lasting, great for modern buildings.
These panels can be made in different sizes and materials for needs.
What Are Explosion-Proof Buildings?

Definition and Purpose
Explosion-proof buildings are made to handle strong explosion forces. They aim to keep people, equipment, and places safe in risky areas. These buildings reduce damage by spreading out the blast energy. Groups like the Unified Facility Criteria (UFC) and General Services Administration (GSA) give rules for building them. The UFC sets basic anti-terrorism rules, while the GSA focuses on walls that resist blasts. New studies look at materials like cross-laminated timber (CLT) for small blasts. This opens up new ways to build safer structures.
Key Features and Materials
These buildings have special features to handle blast pressure. Unlike earthquake designs, they deal with forces pushing outward. Important materials include ceramics that absorb shocks, carbon fiber systems, and spray-on polymers for extra safety. Concrete panels with energy-absorbing layers work even better. These panels can cut movement by 22% and speed by 86%. Tests and studies prove their success. These improvements help meet the needs of blast-prone areas.
Applications in High-Risk Environments
Explosion-proof buildings are vital in dangerous places like chemical plants and military bases. These areas face risks from accidents or attacks. In chemical plants, they protect workers and tools from blasts. In refineries, they keep operations running by reducing damage. Studies show concrete panels lower movement by 22% and speed by 86%. Using advanced sandwich panels, these buildings ensure safety in tough conditions.
Challenges in Explosion-Proof Construction
Handling Blast Loads and Shockwaves
Designing buildings to handle blasts is very challenging. Blast forces create strong pressure that can harm structures. Research shows that joints in tall buildings, like beam connections, are weak under blasts. Masonry walls also struggle with these forces and need special fixes to stay safe.
Concrete panels help solve these problems. Tests with TNT explosions and computer models show they reduce shockwave effects. These panels stop vibrations from spreading, protecting buildings from inside blasts. But designing for blasts means checking every part, like windows. Windows are weak spots, so using strong materials and smaller windows can prevent injuries from broken glass.
Problems with Old Materials
Old materials like steel and concrete are not always good for blasts. They are strong but cannot absorb energy well. Studies show masonry walls need special designs to bend without breaking during blasts. Also, building connections in masonry make designing harder, showing the limits of these materials.
New materials, like metal and polymer foams, work better in many cases. These light materials lower energy transfer during blasts, making buildings stronger. Tests show sandwich panels with aluminum foam handle blasts better than steel or concrete. This makes them great for fixing old buildings or building new ones.
Why Advanced Sandwich Panels Are Needed
To fix the problems with old materials, advanced sandwich panels are needed. These panels absorb energy well, making them great for blast protection. Research shows aluminum sandwich panels with strong fabrics stop high-speed impacts. They are great for safety in risky places.
Expert Malcolm Foster says sandwich panels stop bending and make designs easier. Panels with tubes inside protect well against flying objects. These advanced designs give better blast safety and stronger buildings.
What Are Sandwich Panels?
Structure and Composition
Sandwich panels are special materials used in strong buildings. They have three layers: two outer sheets and a middle core. The outer sheets, often made of steel or aluminum, make the panel strong. The middle core, like foam or honeycomb, absorbs energy and reduces force.
The thickness of these layers affects how they work. Thicker sheets resist blasts better. A denser core absorbs more energy. For example, panels with an aluminum foam core and steel sheets are both strong and light. These panels can lower peak acceleration by 50% compared to steel plates. This makes them great for explosion-proof buildings.
Specification | Description |
---|---|
Core Material | Aluminum foam core with steel face sheets |
Energy Absorption | More foam thickness means better energy absorption |
Peak Acceleration Reduction | Lowers peak acceleration by 50% compared to steel plates |
Blast Resistance | Composite sheets are stronger than metal-only sheets |
Strain Rate Impact | Helps understand crushing and energy absorption |
Face Sheet Thickness | Thicker sheets improve blast resistance |
Key Properties of Sandwich Panels
Sandwich panels have many features that make them useful. They are strong and stay safe under high pressure. They also keep buildings warm and quiet. Fire resistance is important for risky places.
Property Type | Description |
---|---|
Fire Resistance | |
Sound Insulation | Mineral wool blocks noise, great for many buildings. |
Thermal Insulation | Helps keep indoor temperatures steady. |
These panels absorb energy well, which helps during blasts. Panels with composite sheets resist blasts better than metal ones. This makes them a top choice for modern buildings.
Types of Core Materials and Their Benefits
The core material in sandwich panels changes how they work. Different cores have different strengths:
Mineral Wool: Great for fire safety and blocking noise.
Polyurethane Foam: Keeps heat in, saving energy.
Polystyrene: Good for insulation and costs less.
Metallic Foams: Absorb energy well, perfect for blasts.
Graded Polymeric Cores: Absorb more energy, safer for impacts.
The right core depends on the building’s needs. Lightweight polymeric cores are cheap and easy to make. They work well for low-impact uses.
The Role of Sandwich Panels in Explosion-Proof Buildings
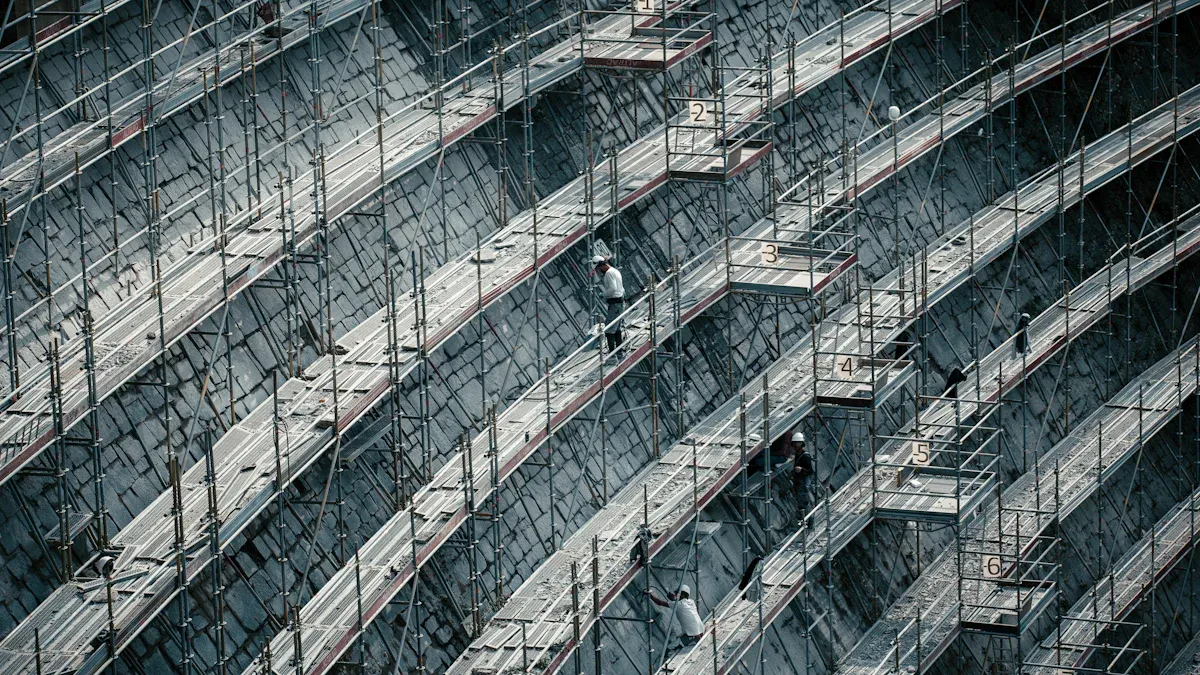
Improving Blast Protection and Energy Absorption
Sandwich panels are very important for explosion-proof buildings. They help protect against blasts and absorb energy well. These panels have two strong outer layers and a light core. This design helps them soak up and spread out blast energy. It reduces damage and keeps people safe.
Studies show how well sandwich panels handle explosions. One study showed concrete panels lower explosion impacts a lot. Another study found metallic panels are great for absorbing energy in risky places.
Study Title | Findings |
---|---|
Verification of Protection Performance of Concrete Blast-Proof Panels Against Internal Explosions | Shows how energy-absorbing materials in panels reduce explosion effects. |
Blast Test and Failure Mechanisms of Soft-Core Sandwich Panels for Storage Halls Applications | Metallic panels work as lightweight energy absorbers for blasts. |
These panels are key to keeping buildings strong during explosions. They handle high-pressure shockwaves, improving safety and performance.
Uses in Building Design
Sandwich panels are used in many parts of explosion-proof buildings. They can be in walls, roofs, and floors. These panels make buildings safer and stronger against crashes.
Advanced core materials like aluminum foam improve energy absorption. For example, hourglass lattice cores work better than older designs in underwater blast tests. This makes them useful for factories and military bases.
Core Structure | Material | Testing Method | Performance Comparison |
---|---|---|---|
Hourglass Lattice | Stainless Steel | Underwater Blast Test | Handles impacts better than pyramidal panels. |
Pyramidal Lattice | Stainless Steel | Underwater Blast Test | Weaker impact performance than hourglass cores. |
Real-Life Examples of Sandwich Panels
Real examples show how sandwich panels work in explosion-proof buildings. Panels with E-glass fiber and PVC foam cores absorb energy well in blast tests. Glass fiber panels with SAN foam cores are also very strong against blasts.
Material Configuration | Testing Method | Key Findings |
---|---|---|
E-glass fiber reinforced vinyl ester face sheets with PVC foam cores | Blast loading | Energy absorption included delamination and fiber breaking. |
Glass fiber reinforced panels with PVC, PMI, and SAN foam cores | Air blast testing | SAN core was the strongest, improving blast resistance. |
These examples prove sandwich panels are great for handling impacts. They make explosion-proof buildings safer and longer-lasting.
Advantages of Using Sandwich Panels
Cost-Effectiveness and Durability
Sandwich panels are a cheaper option for strong buildings. Their light weight lowers transport and setup costs. You spend less on workers and materials but still stay safe. These panels last longer because they resist water, heat, and rust. Unlike older materials, they work well even in tough weather. This strength cuts repair costs and keeps them reliable for years.
Tests show panels with advanced cores, like aluminum foam, handle impacts better. This makes them perfect for risky places. They absorb energy well, so fewer repairs are needed after blasts. Choosing sandwich panels means saving money while getting great performance.
Versatility in Design and Construction
Sandwich panels fit many building needs. You can change their size, thickness, or core material. Pick the right type for insulation, soundproofing, or blast safety. This makes them useful for walls, roofs, and floors in strong buildings.
Their light weight makes building easier and faster. You can install them quickly, saving time on projects. They also work well with other materials. This lets you create cool designs without losing safety. For example, honeycomb cores resist impacts and look nice too.
Comparison to Traditional Materials
Old materials like concrete and steel don’t work as well. Concrete is heavy and doesn’t absorb blasts well. Steel is strong but bad at handling impacts or keeping heat in. Sandwich panels mix the best parts of both. They resist blasts but stay light and easy to use.
For example, panels with metallic foam cores absorb energy better than steel. They spread out shockwaves, keeping buildings and people safe. Switching to sandwich panels improves safety, saves time, and allows creative designs.
Explosion-proof buildings are crucial for keeping people and property safe. Using advanced materials like sandwich panels boosts blast protection and absorbs energy better. These panels make buildings safer and allow flexible designs.
🛠️ Future Potential: Sandwich panels are great for modern construction. They are light, strong, and save energy, making them perfect for today’s needs.
When looking for safer building methods, sandwich panels are a smart and dependable choice for current and future challenges.
FAQ
Why are sandwich panels better than older materials for explosion-proof buildings?
Sandwich panels soak up energy better than concrete or steel. They are light, which cuts transport costs and speeds up building. They also insulate and block noise well, making them useful in many ways.
Can sandwich panels be made to fit special building needs?
Yes, sandwich panels can be changed in size, thickness, or core. This lets them meet needs like keeping heat in, blocking sound, or stopping blasts, based on what the building needs.
Are sandwich panels good for the environment?
Many sandwich panels use recyclable materials like aluminum or steel. Some cores, like polyurethane foam, save energy by keeping heat inside. This makes them a greener choice for building today.
How do sandwich panels hold up in bad weather?
Sandwich panels stand up to water, heat, and rust, so they last. They keep indoor spaces warm or cool and have fire-safe cores like mineral wool for risky places.
Where are sandwich panels used in explosion-proof buildings?
Sandwich panels are used in walls, roofs, and floors. They work well in places like chemical plants, military bases, and storage sites where safety from blasts is key.
🛠️ Tip: Talk to experts to pick the best sandwich panel. The core and outer layers should match your building’s safety and needs.