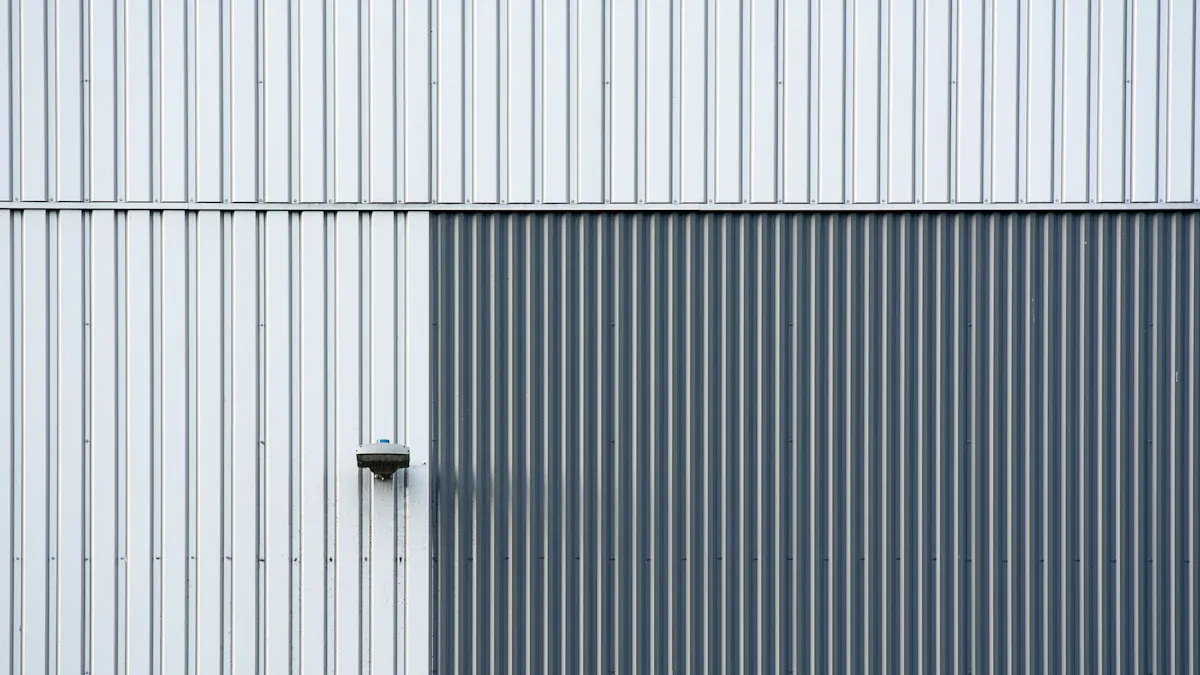
Polyurethane (PU) sandwich panels are modern building materials known for their excellent insulation and strong structure. These panels feature a foam core in the middle, which is sandwiched between tough outer layers like steel or aluminum. This design provides good heat insulation, light weight, and strength. Conducting material analysis is important to evaluate how well these panels perform, ensuring they are suitable for various applications. They are particularly useful for factories, energy-saving homes, and clean rooms, all of which require materials that function effectively.
Key Takeaways
PU sandwich panels are light and strong, perfect for building and transport.
The foam inside keeps heat or cold in, saving energy and money.
Metal layers like steel or aluminum protect the foam and make panels tough against weather and fire.
These panels can last 30 to 40 years, making them a good long-term choice for buildings and factories.
Panels can be customized to fit different needs, so they work well for many uses.
Materials in Polyurethane Sandwich Panels
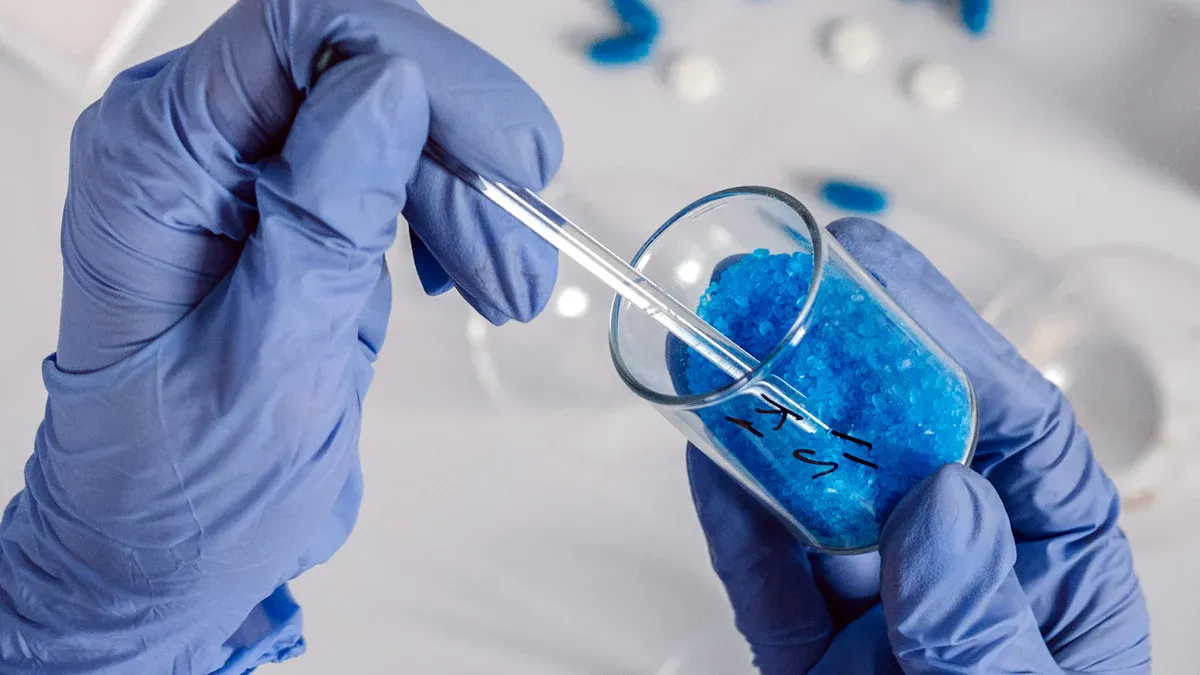
Polyurethane Foam Core
Properties of polyurethane foam
Polyurethane foam is the middle layer in sandwich panels. It provides great heat insulation and strong support. Its light weight makes the panel easier to handle but still tough. The foam resists being squished under heavy weight. Its tiny closed cells keep water out, making it last longer in wet places.
Property | Value |
---|---|
Flexural Strength | 3.68 MPa |
Compressive Strength | 15.53 MPa |
Tensile Strength | 0.175 MPa |
Flexural Strain | 77.33% higher than EPS |
These features make polyurethane foam a good choice for strong and energy-saving materials.
Types of polyurethane foam used
Different kinds of polyurethane foam are used for different jobs. Rigid foam is great for keeping heat out and handling heavy weight. Flexible foam is better for soft padding and absorbing hits. Both types make sandwich panels useful in many industries.
Outer Layers in Sandwich Panels
Common materials (e.g., steel, aluminum)
The outside layers of sandwich panels are often made of steel or aluminum. These materials make the panel strong and protect the foam inside. Steel-polyurethane-steel (SPS) panels are popular because they are tough and resist weather damage.
Role in structural performance
The outer layers make the panel stronger and last longer. They shield the foam core from damage and bad weather. They also help the panel handle bending and heavy loads without breaking.
Description | |
---|---|
Compressive Strength | Handles heavy weight without breaking, important for shrinkage. |
Bending Strength | Measures how much bending the panel can take before breaking. |
Bonding Strength | Shows how well the foam sticks to the steel without coming apart. |
Adhesive Layer in Panels
Purpose of adhesive in bonding
The adhesive layer sticks the foam core to the outer layers. This keeps the panel strong and in one piece. A good adhesive stops the layers from peeling apart, which could weaken the panel.
Types of adhesives used
Different adhesives are chosen based on what the panel will be used for. Polyurethane adhesives work well with the foam core. Epoxy adhesives are strong and resist weather damage. These adhesives make the panel more durable and dependable.
Findings | |
---|---|
Energy Release Rate (GII) | Thinner cores release energy differently than thicker ones when cracks form. |
De-lamination Impact | Small cracks in thin cores are less harmful than in thick ones. Adhesives help prevent these problems. |
Material Analysis of PU Sandwich Panels
Thermal Properties
How polyurethane keeps heat in or out
Polyurethane, used in sandwich panels, stops heat from passing through. This makes it a great material for keeping spaces warm or cool. Its foam core has tiny air pockets that trap air. These air pockets help block heat, making it perfect for cold storage and temperature-controlled places.
Saving energy with better insulation
Polyurethane panels save energy by keeping buildings warm or cool. They lower the need for heating or cooling, cutting costs and helping the environment. The market for these panels is growing fast. It could rise from $9.5 billion in 2023 to $16.8 billion by 2032. This shows how important they are for saving energy in modern buildings.
Mechanical Properties
Strength to handle heavy weight
Polyurethane panels are strong and can hold heavy loads. This makes them great for roofs and floors. Studies show their strength reaches 15.53 MPa, which is good for tough jobs.
Strength to resist pulling apart
These panels can handle pulling forces without breaking. Their tensile strength is 0.175 MPa, making them durable. This helps them stay strong in many uses.
How layers stick together
The glue in these panels keeps the layers stuck together. Strong glue stops the layers from peeling apart under pressure. Better glue makes the panels stronger and more reliable for building use.
Performance Metric | Result |
---|---|
Maximum Flexural Load | 506% higher |
Initial Flexural Stiffness | 816% higher |
Impact Energy Absorption | 21% higher |
Fire Resistance
Making polyurethane safer from fire
Polyurethane foam can be treated to resist fire. These treatments slow down flames, making buildings safer. But untreated foam burns easily, so fire-resistant versions are important.
Outer layers help stop fire
The steel or aluminum outer layers help block fire. They slow flames and protect the foam inside. Tests like ISO 13784-1:2014 and EN 13501-1:2019 prove these panels meet fire safety rules.
Standard | What It Tests |
---|---|
ISO 13784-1:2014 | Checks how panels handle fire. |
EN 13501-1:2019 | Rates fire safety for building parts. |
EN 13823:2020 | Tests panels on a medium scale for fire safety. |
UNE-EN 14509:2014 | Sets rules for insulated panels with CE marks. |
Factors That Change Material Properties
What Materials Are Made Of
Mixing isocyanate and polyol in polyurethane
The mix of isocyanate and polyol changes how polyurethane works. Changing this mix affects the foam’s strength, flexibility, and density. More isocyanate makes the foam stronger for heavy loads. Studies show this mix also changes how well the foam sticks together and lasts.
Aspect | How It Affects Strength |
---|---|
Material Mix | Different isocyanate and polyol mixes change strength. |
Catalyst Use | Good catalyst use makes the foam stronger. |
Foaming Agent Amount | Less foaming agent makes the foam tougher. |
Picking the right outer materials
The outer layers decide how strong the panel is. Steel and aluminum are common choices because they last long and resist damage. Steel is strong for heavy loads, while aluminum is light and flexible. These layers protect the foam and make the panel last longer.
How Panels Are Made
Heat and pressure during making
Heat and pressure affect how good the panels are. The right heat helps the foam set properly, making it stronger.
Keeping the right heat makes the foam react well and strong. The metal’s heat level also affects how fast the foam sets.
Pressure helps stick the foam to the outer layers evenly. Enough pressure stops the layers from peeling apart and keeps the panel strong.
Machines and tools used
Better machines make better panels. Special tools like corona treatment and glue improve how layers stick.
Using corona and glue on steel plates makes them stick better. This cleans the surface and helps the glue hold tight, keeping the panel strong.
Modern machines control heat and pressure well, making all panels equally strong.
Effects of the Environment
How weather changes affect panels
Weather like humidity and heat can weaken panels. Too much humidity can hurt the glue, making layers come apart. Extreme heat or cold can make the panel expand or shrink. Picking the right materials and making them well can stop these problems.
Staying strong in tough conditions
Polyurethane panels last well in different weather. Their foam keeps water out, and the outer layers protect the inside. This makes them great for heavy-duty jobs and tough environments.
Core Material | Compressive Strength (MPa) | Tensile Strength (MPa) | |
---|---|---|---|
PU Foam | 3.68 | 15.53 | 0.175 |
EPS | N/A | N/A | N/A |
Applications of Polyurethane Sandwich Panels
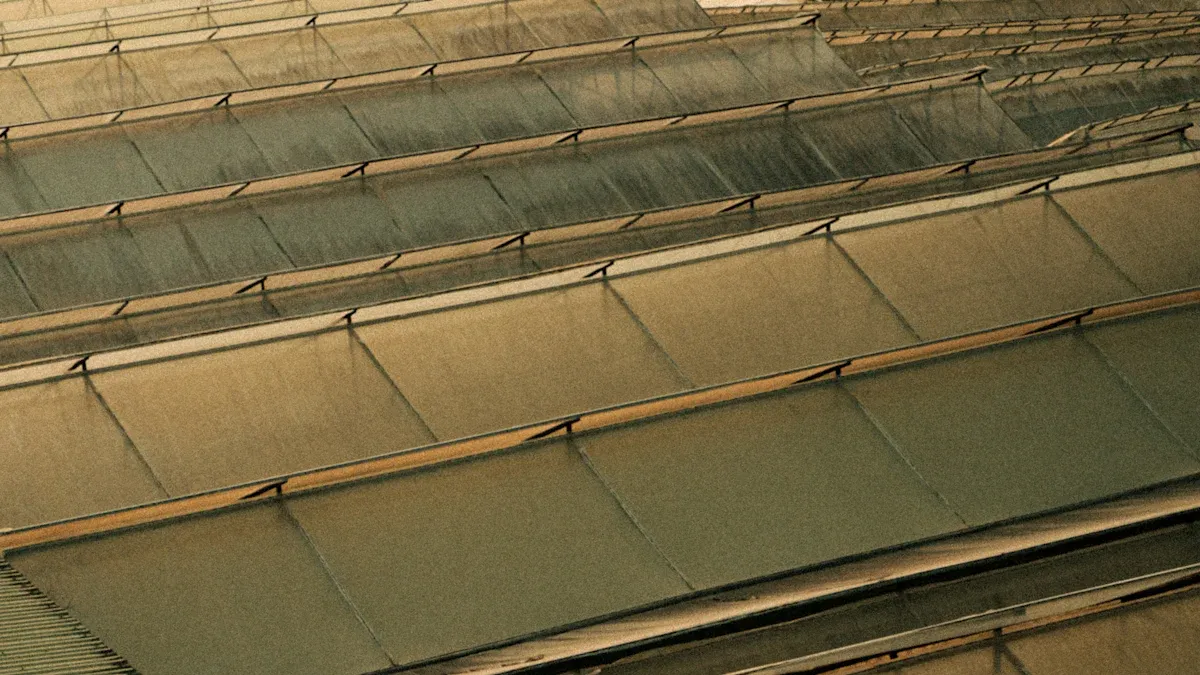
Construction Industry
Use in walls, roofs, and cold storage
Polyurethane sandwich panels are important in modern construction. They provide great insulation and are very durable. These panels are used in walls and roofs because they are light. Their lightweight design makes them easy to install and saves time. The strong honeycomb core adds strength for homes and buildings.
In cold storage, these panels keep temperatures steady inside. The honeycomb core stops heat from moving through, saving energy. This lowers costs and makes them efficient. They last 30 to 40 years and use recycled steel, helping the environment. Cold storage needs these panels for good refrigeration performance.
Key benefits of these panels include:
Great insulation
Energy savings
Easy to install
Long-lasting
Industrial Applications
Applications in warehouses and factories
Factories and warehouses use these panels for tough jobs. They handle heavy loads and harsh conditions well. The honeycomb core makes them strong and reliable. Their light weight reduces stress on buildings, perfect for big projects.
Industries use these panels for energy savings and fire safety. They keep heat in or out and resist fire, making them safe. Clean rooms and labs also use them because they meet strict standards.
Sector | Applications | |
---|---|---|
Agricultural | Need for fireproof and chemical-resistant materials. | |
Residential | Building energy-saving homes | Demand for eco-friendly and affordable housing. |
Commercial | Offices, shops, and hotels | Need for quick and energy-efficient building materials. |
Industrial | Factories and warehouses | Focus on saving energy and fast industrial growth. |
Niche Applications | Labs, clean rooms, and special buildings | Need for high-quality, custom materials. |
Transportation Sector
Use in refrigerated vehicles and containers
The transport industry depends on these panels for cold storage. They keep goods fresh by maintaining steady temperatures. The honeycomb core stops heat transfer, making them great for cooling.
These panels also block UV rays, improving their use in transport. Their light weight saves fuel, cutting costs and helping the planet. More refrigerated transport means these panels are needed for food and sensitive items.
Their insulation makes them a top choice for transport. They are strong and last long, even in tough conditions.
Polyurethane sandwich panels have a strong foam center and tough outer layers. These layers, made of polyurethane foam, steel, or aluminum, make the panels strong and good at keeping heat in or out. They also resist fire and handle heavy weight well. Tests show they save energy and meet safety rules.
Key takeaway: PU sandwich panels are very useful for building, factories, and transport.
Knowing how these panels work helps industries use them better. This ensures they last long and fit many tough jobs.
FAQ
What are the main advantages of PU sandwich panels?
PU sandwich panels are lightweight, strong, and save energy. They keep heat in or out and resist fire. These qualities make them great for buildings, factories, and transport.
How long do PU sandwich panels typically last?
PU sandwich panels can last 30 to 40 years. Their lifespan depends on good care, materials, and weather conditions.
Are PU sandwich panels environmentally friendly?
Yes, PU sandwich panels help save energy by reducing heating and cooling. Many use recycled steel and last long, creating less waste.
Can PU sandwich panels be customized for specific applications?
Yes, manufacturers can change the foam core, outer layers, or size. This makes them useful for different jobs like building or transport.
How do PU sandwich panels perform in extreme weather?
PU sandwich panels work well in tough weather. The foam core blocks water, and the outer layers handle heat or cold. They are perfect for places like cold storage or hot areas.
Tip: Check panels often to keep them working well in bad weather.